Abstract: The traditional injection molding machine oil pump motor consumes 80% of the power consumption of the equipment. To reduce the energy consumption of the injection molding machine, the energy consumption of the oil pump motor is mainly reduced. The conversion of the oil pump motor into an electric-hydraulic servo motor can be very ideally achieved. The goal of saving electricity. CA500 series heavy-duty servo driver can be used with electro-hydraulic injection molding servo expansion card to drive CM500 series permanent magnet synchronous motor. It is used in electro-hydraulic injection molding machine servo matching and transformation.
Keywords: Injection Molding Machine, Energy Saving, Retrofit, Servo, CA500, CM500
First, the injection molding machine principle and process description Injection molding machine is a special plastic molding machine. It uses plastic thermoplastic, after appropriate heating and melting, adding high pressure quickly into the mold, after a certain period of pressure, cooling, a variety of profiles and plastic products.
A working cycle of the injection molding machine includes the following operations:
(1) Closing the mold: When the template quickly approaches the fixed template and confirms that no foreign matter is present, the system turns to high pressure and the template is locked;
(2) Injection table advance: nozzle and mold close;
(3) Injection: The injection screw injects the molten material at the front of the cartridge into the mold cavity with a certain pressure and speed;
(4) Pressure maintenance and cooling: Through this action, the plastic products in the cavity are cooled and formed;
(5) Pre-molding: The hydraulic motor is conventionally used to drive the screw and retreat, and the plastic particles added in the hopper are pushed forward for pre-molding. The screw retreats to a predetermined position, stops rotating, and prepares for the next injection;
(6) Injection station retreats, open mold;
(7) Top products.
The hydraulic system generates pressure and flow through the cooperation of the oil pump and different valves, providing the required driving force and moving speed of the cylinder and the hydraulic motor.
Second, the injection molding machine common program comparison 1, the traditional injection molding machine system program:
Traditional quantitative pump injection molding machine is the use of quantitative pump oil injection, the injection process of the various actions on the speed, pressure requirements are not the same, it is through the injection molding machine proportional valve using overflow adjustment method bypass excess oil bypass flow tank In the whole process, the rotation speed of the motor is constant, so the fuel supply is also fixed, and because the execution action is intermittent, it is not possible to be full load, so the quantitative oil supply wastes a lot of energy. .
2, frequency conversion program:
The frequency conversion reformation scheme is more energy-efficient than the conventional fixed-displacement pump scheme. The current/pressure signal of the proportional flow valve is input to the analog input of the frequency converter at the same time. By controlling the rotation speed of the oil pump motor, the actual flow of the oil pump is proportional to the rotation speed of the motor. The power is therefore also proportional to the speed of the motor, which serves the purpose of energy saving, and its energy saving effect ranges from 25% to 50%.
3, synchronous servo transformation program:
The principle of the servo modification scheme is different from that of scheme 2 on the oil pump. The scheme 2 is driven by the ordinary asynchronous motor and frequency converter, and the servo pump oil pump drive is composed of permanent magnet synchronous servo motor and servo driver (Fig. 1)
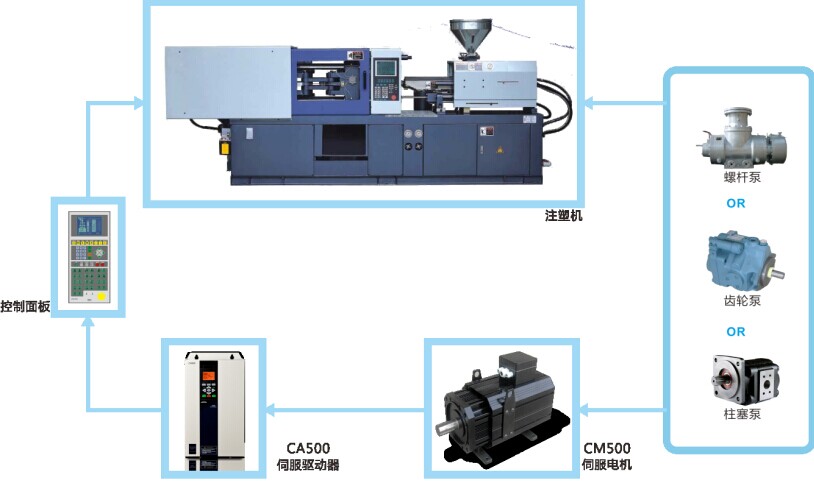
Synchronous servo scheme has the advantages of high energy-saving rate, high efficiency and high yield as compared with ordinary frequency conversion asynchronous motor drive scheme:
Servo drive combined with synchronous servo motor, low-frequency torque, high speed accuracy, higher product stability;
The servo drive system has a fast dynamic response and a small torque response time, improving process efficiency.
Real-time detection of pressure feedback, response to pressure, flow adjustment, the output power of the motor and its load match, and the entire process of the injection molding machine is completely consistent, without affecting the production efficiency under the premise of achieving high efficiency and energy saving;
Synchronous motor rotor without excitation, large output per ampere, more energy-saving;
Servo-driven motor hydraulic energy consumption than traditional injection molding machine energy-saving 30 to 70%.
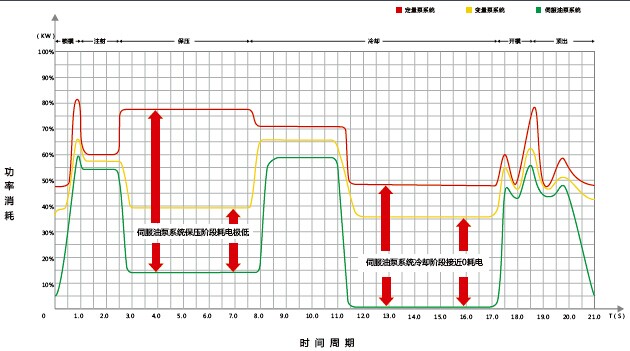
Third, the Quartet servo injection molding machine program Synchronous servo oil pump system injection molding machine program, to CA500 series heavy-duty servo drive as the control platform, with electro-hydraulic injection servo dedicated adapter card and resolver adapter, and CM500 synchronous motor composition Servo closed loop control system.
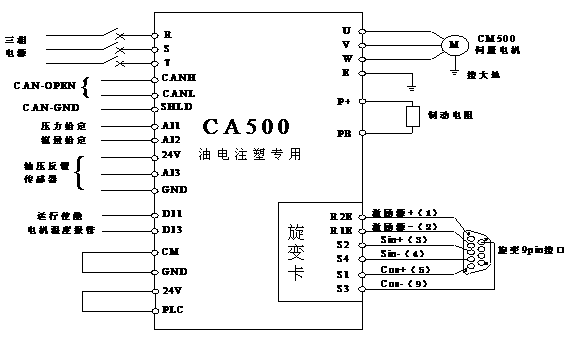
Four-party servo injection molding machine program features 1, CA500 servo drive features:
CA500 servo drive combined with CM500 synchronous servo motor, low-frequency torque, 0.5HZ can reach 220% of the rated torque;
The CA500 servo driver has a fast dynamic response, the torque response time is less than 5ms, and the steady speed accuracy reaches ±0.02%.
For the injection molding machine in a specific process of short-term high-current impact requirements, CA500 uses a large margin of heavy load design, rated load 120% long-term operation, 160% for 60 seconds, 200% for 1 second;
Full range of built-in brake units save installation space and external brake unit costs;
The PID module developed for the electro-hydraulic servo injection molding machine precisely controls the oil pressure and the pressure fluctuation is less than ±0.5 bar, maintaining the pressure of the system quickly, accurately and steadily to reach the set pressure and flow;
Extensible open platform design, standard CAN communication interface, a variety of communication protocol formats, adapt to various injection molding machine computer systems;
The system has a multi-pump confluence and a multi-pump shunt control function, which can minimize the system cost, shorten the user's product process cycle, and improve efficiency;
Simplified debugging function (free adjustment of the square motor), the largest program to reduce customer debugging parameters, easy installation and use.
2, CM500 AC permanent magnet servo motor features:
CM500 servo motor has low noise, small vibration and inertia, fast response, stable operation, compact structure, and high power density;
CM500 motor uses high-performance rare earth permanent magnet material, anti-demagnetization ability. The rotor of the motor adopts a special structure and technology. The enclosure protection class is IP54 and the insulation class is Class F, which ensures the reliability of the motor during operation.
The use of a rugged brushless rotary transformer as a feedback element can adapt to harsh environments such as high temperature, vibration, dust, and oil.
IV. Summary This article introduced a kind of application based on the quadrilateral CA500 series heavy-duty servo driver and CM500 synchronous servo motor in the injection molding machine servo system. This program has highly efficient power-saving function, and its energy-saving rate can reach 40~90%. And the system response is quick, the operation is stable and reliable, the protection function is powerful, and the operation is simple and convenient. It can not only meet the requirements of injection molding process, improve product quality and output, but also reduce equipment maintenance costs, and create good economic benefits for users. Has been successfully applied to a number of injection molding machine servo applications.
References 1, "CA500 series heavy-duty servo drive manual V1.1" Shenzhen Sifang Electric Technology Co., Ltd. 2, "CM500 series AC permanent magnet servo motor user manual V1.0" Shenzhen Sifang Electric Technology Co., Ltd. 3, " Electro-hydraulic Servo Extension Card Instruction Manual V1.2》Shenzhen Sifang Electric Technology Co., Ltd.
Keywords: Injection Molding Machine, Energy Saving, Retrofit, Servo, CA500, CM500
First, the injection molding machine principle and process description Injection molding machine is a special plastic molding machine. It uses plastic thermoplastic, after appropriate heating and melting, adding high pressure quickly into the mold, after a certain period of pressure, cooling, a variety of profiles and plastic products.
A working cycle of the injection molding machine includes the following operations:
(1) Closing the mold: When the template quickly approaches the fixed template and confirms that no foreign matter is present, the system turns to high pressure and the template is locked;
(2) Injection table advance: nozzle and mold close;
(3) Injection: The injection screw injects the molten material at the front of the cartridge into the mold cavity with a certain pressure and speed;
(4) Pressure maintenance and cooling: Through this action, the plastic products in the cavity are cooled and formed;
(5) Pre-molding: The hydraulic motor is conventionally used to drive the screw and retreat, and the plastic particles added in the hopper are pushed forward for pre-molding. The screw retreats to a predetermined position, stops rotating, and prepares for the next injection;
(6) Injection station retreats, open mold;
(7) Top products.
The hydraulic system generates pressure and flow through the cooperation of the oil pump and different valves, providing the required driving force and moving speed of the cylinder and the hydraulic motor.
Second, the injection molding machine common program comparison 1, the traditional injection molding machine system program:
Traditional quantitative pump injection molding machine is the use of quantitative pump oil injection, the injection process of the various actions on the speed, pressure requirements are not the same, it is through the injection molding machine proportional valve using overflow adjustment method bypass excess oil bypass flow tank In the whole process, the rotation speed of the motor is constant, so the fuel supply is also fixed, and because the execution action is intermittent, it is not possible to be full load, so the quantitative oil supply wastes a lot of energy. .
2, frequency conversion program:
The frequency conversion reformation scheme is more energy-efficient than the conventional fixed-displacement pump scheme. The current/pressure signal of the proportional flow valve is input to the analog input of the frequency converter at the same time. By controlling the rotation speed of the oil pump motor, the actual flow of the oil pump is proportional to the rotation speed of the motor. The power is therefore also proportional to the speed of the motor, which serves the purpose of energy saving, and its energy saving effect ranges from 25% to 50%.
3, synchronous servo transformation program:
The principle of the servo modification scheme is different from that of scheme 2 on the oil pump. The scheme 2 is driven by the ordinary asynchronous motor and frequency converter, and the servo pump oil pump drive is composed of permanent magnet synchronous servo motor and servo driver (Fig. 1)
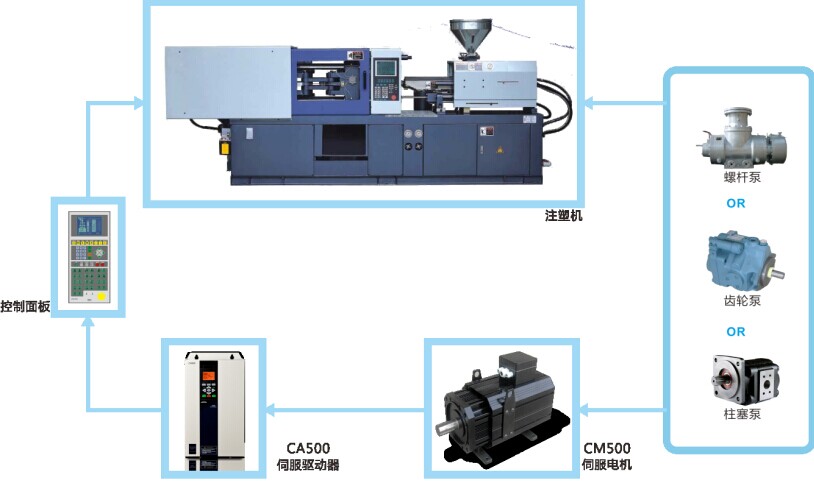
Figure 1 injection molding machine synchronous servo program
Synchronous servo scheme has the advantages of high energy-saving rate, high efficiency and high yield as compared with ordinary frequency conversion asynchronous motor drive scheme:
Servo drive combined with synchronous servo motor, low-frequency torque, high speed accuracy, higher product stability;
The servo drive system has a fast dynamic response and a small torque response time, improving process efficiency.
Real-time detection of pressure feedback, response to pressure, flow adjustment, the output power of the motor and its load match, and the entire process of the injection molding machine is completely consistent, without affecting the production efficiency under the premise of achieving high efficiency and energy saving;
Synchronous motor rotor without excitation, large output per ampere, more energy-saving;
Servo-driven motor hydraulic energy consumption than traditional injection molding machine energy-saving 30 to 70%.
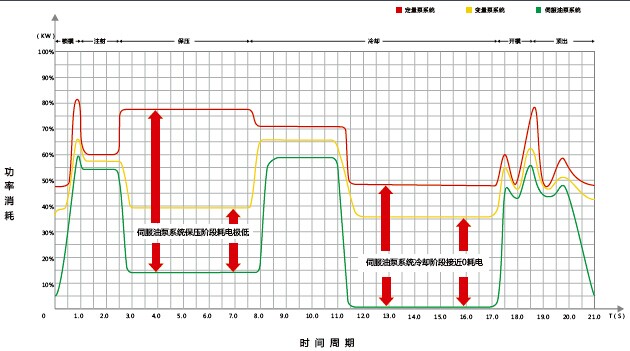
Figure 2 Comparison of Energy Savings for Three Oil Pump Solutions
Third, the Quartet servo injection molding machine program Synchronous servo oil pump system injection molding machine program, to CA500 series heavy-duty servo drive as the control platform, with electro-hydraulic injection servo dedicated adapter card and resolver adapter, and CM500 synchronous motor composition Servo closed loop control system.
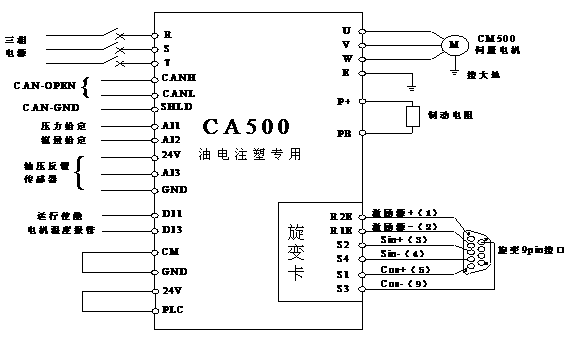
Figure 3 Electrical wiring diagram of servo system
Four-party servo injection molding machine program features 1, CA500 servo drive features:
CA500 servo drive combined with CM500 synchronous servo motor, low-frequency torque, 0.5HZ can reach 220% of the rated torque;
The CA500 servo driver has a fast dynamic response, the torque response time is less than 5ms, and the steady speed accuracy reaches ±0.02%.
For the injection molding machine in a specific process of short-term high-current impact requirements, CA500 uses a large margin of heavy load design, rated load 120% long-term operation, 160% for 60 seconds, 200% for 1 second;
Full range of built-in brake units save installation space and external brake unit costs;
The PID module developed for the electro-hydraulic servo injection molding machine precisely controls the oil pressure and the pressure fluctuation is less than ±0.5 bar, maintaining the pressure of the system quickly, accurately and steadily to reach the set pressure and flow;
Extensible open platform design, standard CAN communication interface, a variety of communication protocol formats, adapt to various injection molding machine computer systems;
The system has a multi-pump confluence and a multi-pump shunt control function, which can minimize the system cost, shorten the user's product process cycle, and improve efficiency;
Simplified debugging function (free adjustment of the square motor), the largest program to reduce customer debugging parameters, easy installation and use.
2, CM500 AC permanent magnet servo motor features:
CM500 servo motor has low noise, small vibration and inertia, fast response, stable operation, compact structure, and high power density;
CM500 motor uses high-performance rare earth permanent magnet material, anti-demagnetization ability. The rotor of the motor adopts a special structure and technology. The enclosure protection class is IP54 and the insulation class is Class F, which ensures the reliability of the motor during operation.
The use of a rugged brushless rotary transformer as a feedback element can adapt to harsh environments such as high temperature, vibration, dust, and oil.
IV. Summary This article introduced a kind of application based on the quadrilateral CA500 series heavy-duty servo driver and CM500 synchronous servo motor in the injection molding machine servo system. This program has highly efficient power-saving function, and its energy-saving rate can reach 40~90%. And the system response is quick, the operation is stable and reliable, the protection function is powerful, and the operation is simple and convenient. It can not only meet the requirements of injection molding process, improve product quality and output, but also reduce equipment maintenance costs, and create good economic benefits for users. Has been successfully applied to a number of injection molding machine servo applications.
References 1, "CA500 series heavy-duty servo drive manual V1.1" Shenzhen Sifang Electric Technology Co., Ltd. 2, "CM500 series AC permanent magnet servo motor user manual V1.0" Shenzhen Sifang Electric Technology Co., Ltd. 3, " Electro-hydraulic Servo Extension Card Instruction Manual V1.2》Shenzhen Sifang Electric Technology Co., Ltd.
China leading manufacturers and suppliers of Flat Gloss Powder Coating,Flat Black Powder Coating, and we are specialize in Powder Coating Gloss,Powder Coating, etc.
Flat Gloss Powder Coating,Flat Black Powder Coating,Powder Coating Gloss,Powder Coating
Longkou Guomei Decoration Material Co.,Ltd. , https://www.ytgmcoating.com