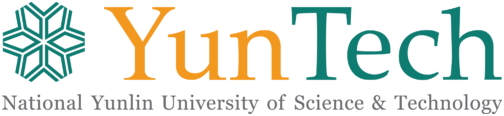
- Customer: Yunlin University of Science and Technology (YunTech)
- Region: Taiwan
- Industry: Academy & Education
- Solution:Â Moldex3D Solution Add-on /Â Co-injection Module
- View PDF Version
Executive Summary
Multi-component molding (MCM) has been applied in industries for many decades. However, due to the complicated combinations from materials to processes, it is very difficult to control and manage this type of product development. Â In this case, YunTech has extended their study from over-molding to co-injection molding to find out the physical mechanism of product warpage. Â In over-molding MCM system, because of the imbalanced in volume shrinkage and heat accumulation or dissipation, warpage can be inward or outward. Â The final warpage quality can be managed and controlled. Â On the other hand, in co-injection MCM system, warpage is strongly affected by the core penetration distance. Â In this study, if the core penetration is greater than the critical value, warpage can be improved. Â With the help of Moldex3D, YunTech found the optimal process conditions and solved this warpage issue. Â YunTech Team will apply the result for guiding future research on multi-material co-injection molding.
Challenges
- Control molding parameters including material properties, core/skin ratio and process conditions in co-injection process
- Warpage
- Control the product size precision
Solutions
Utilizing Moldex3D Co-injection module to decide the optimum core/skin ratio and process conditions in order to successfully control core penetration and warpage
Benefits
- Reduce warpage by 53%
- Predict warpage factors before actual molding and avoided unnecessary molding costs
- Develop a competitive edge in the market
Case Study
This project’s specific objectives primarily focus on warpage improvement and to find out the physical mechanism behind this quality improvement.  To better understand the sequential co-injection molding processes, YunTech decided to utilize Moldex3D software.  The geometrical model of the product includes runner system and dimensions as shown in Fig. 1.  To evaluate the warpage variation, the definition of warpage is shown in Fig. 2.  As shown in the picture, S0 is the original designed length.  At Corner A, when S1<S0, the warpage is inward.  At Corner B, when S2<S0, the warpage is also inward.  S2-S1 indicates the warpage trend of two arms.
Fig. 1 The geometrical dimensions of the part
Fig. 2 Definition of inward or outward warpage: (1) At Corner A, when S1<S0, the warpage is inward;
(2) At corner B, when S2<S0, the warpage is also Inward.
Based on the above investigation, the warpage improvement mechanism is due to the criteria of critical core penetration distance (Fig. 3). As the core crosses the red diagonal line, warpage can be improved. In this case, the critical central penetration distance is 36 mm. It means when central core penetration distance is above 36 mm, warpage will be improved. In the original design setting, when the core ratio is larger than 20% (the central core penetration is over 36 mm), the quality will be improved significantly. Based on this, YunTech made the following design changes: (1) Change the core ratio; (2) Reduce the melt temperature; and (3) Reduce the flow rate of the first shot.
Fig. 3 The diagram of critical penetration distance (the distance from the gate to the diagonal line)
As a result, with the help of Moldex3D, YunTech successfully reduced the warpage from 0.792 to 0.378 mm (52.7% significant improvement) by increasing the core/skin ratio (Fig. 4).
Fig. 4 The results of S2-S1 in various core ratios and control factors.
Results
Moldex3D makes it possible to present the core penetration behavior prediction for co-injection applications and successfully solve molding issues. The experimental results also prove the accuracy of Moldex3D (Fig. 5). This result paves the way forYunTech’s application in manufacturing compound products with different materials in the near future.
Fig. 5 The melt behaviour in simulation is very similar with the reality.
Â
Roller Covered Ceramic Adhesive Sheet
Anti-friction ceramic adhesive plate,Non-sanding cold bonded overmolding,Anti-slip ceramic adhesive plate
Hebi Shuanglian Trading Co. , https://www.slwearrubber.com