I. Introduction of Laser Cutting Machine Specifications
In the rapidly evolving field of metal processing, laser cutting machines stand out for their precision, versatility, and efficiency. However, the breadth of available models, each with distinct specifications, can present a challenge even to seasoned professionals.
Understanding the specifications of laser cutting machines is crucial for making informed decisions that align with specific production goals, material types, and desired outcomes.
Knowing the right parameters can significantly enhance productivity, optimize resource utilization, and ensure the finished product meets stringent quality standards.
Laser cutting machines differ not just in their core technology but also in myriad other aspects such as power output, cutting speed, and compatibility with various materials.
Understanding these specifications helps in selecting the right machine, thus avoiding costly mismatches and ensuring seamless operations. It also aids in comprehending the machine's limits and capabilities, leading to better maintenance and longer lifespan.
II. Types of Laser Cutting Machines
Laser cutting machines leverage highly focused laser beams to precisely cut or engrave materials. The primary types of laser cutting machines used in industrial applications are CO2, fiber, and Nd:YAG lasers, each with distinct characteristics, applications, and specifications. Understanding these variations is essential for selecting the right equipment to meet specific manufacturing needs.
CO2 Laser Cutting Machines
CO2 laser cutting machines use a gas mixture primarily composed of carbon dioxide as the lasing medium. These machines are favored for their ability to cut a wide range of materials, including metals, plastics, wood, and textiles.
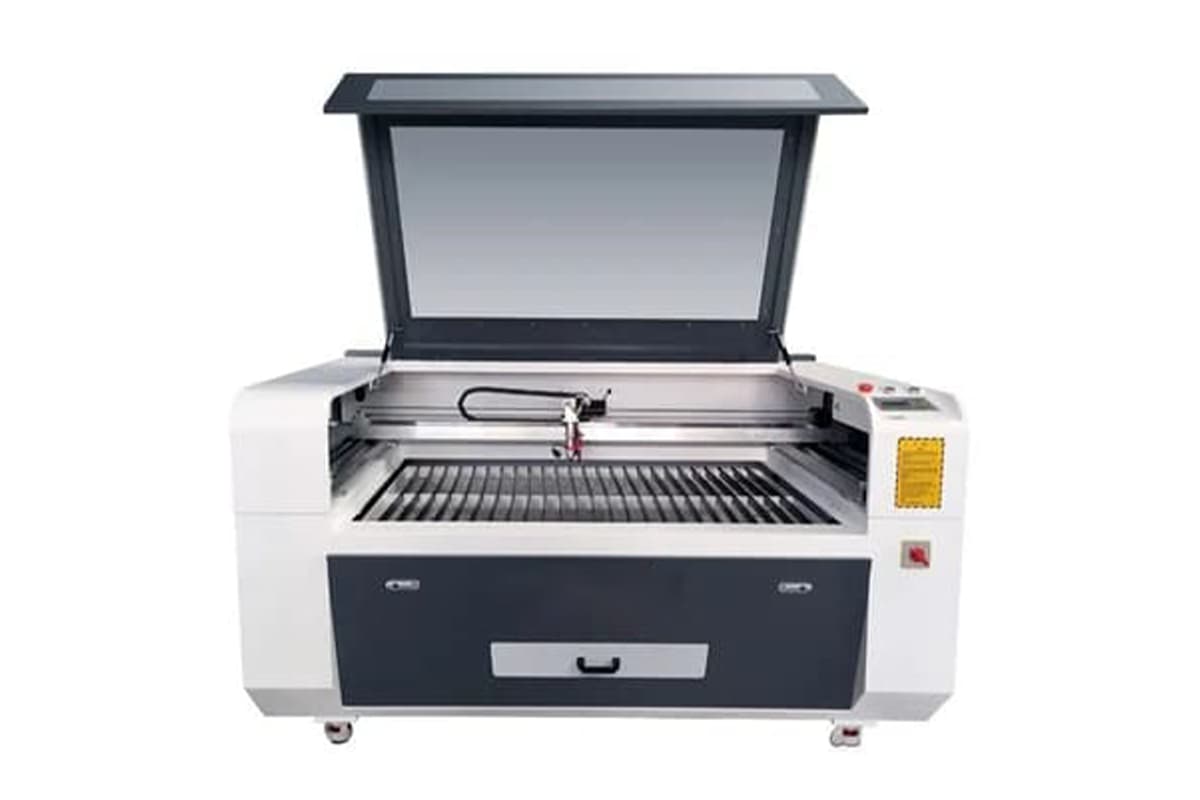
Common Applications
CO2 lasers are commonly used in industries such as automotive manufacturing, aerospace, signage, and apparel. Their versatility makes them suitable for cutting, engraving, and marking both metals and non-metals with high precision.
For instance, they are often employed for cutting stainless steel and aluminum, as well as intricate engraving patterns on organic materials.
Key Specifications
- Power Output: Typically ranges from 20W to several kW, depending on the specific application.
- Cutting Speed: Capable of high-speed cutting, especially effective with thinner materials.
- Beam Quality (M²): CO2 lasers generally offer good beam quality, which determines the fineness of the cut.
- Cooling Method: Often requires water cooling systems to maintain operational temperatures.
- Wavelength: Operates at a wavelength of 10.6 micrometers, ideally suited for non-metallic materials and some metals.
Fiber Laser Cutting Machines
Fiber lasers utilize a solid-state lasing medium, where the laser beam is generated and delivered through an optical fiber. These machines are known for their efficiency, compact size, and effectiveness in cutting reflective materials.
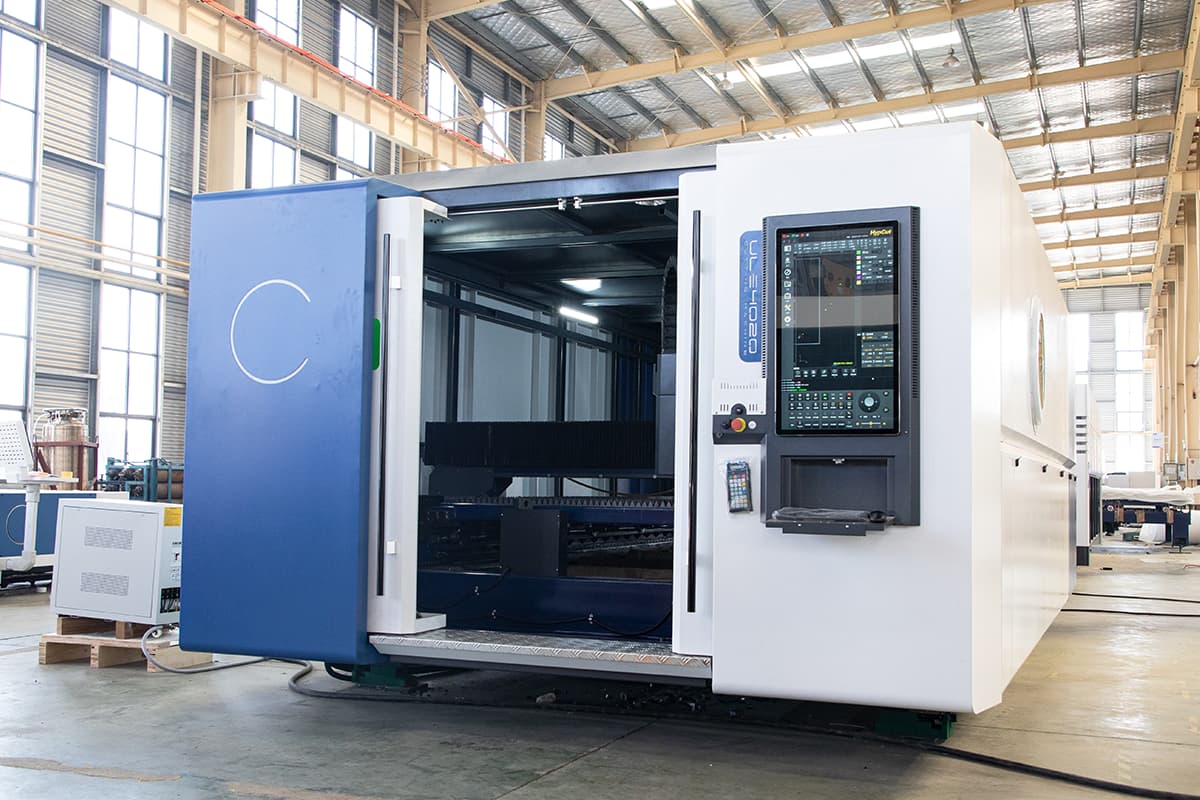
Common Applications
Fiber lasers are predominantly used in industries requiring cutting and engraving of metals. Their high precision and power make them ideal for applications in electronics, medical device manufacturing, and fine metalwork, including cutting copper, brass, and silver, which are typically challenging for CO2 lasers.
Key Specifications
- Power Output: Ranges from 500W to over 10kW, suitable for various thicknesses of metal.
- Cutting Speed: High cutting speed, especially for thin and medium-thickness materials.
- Beam Quality (M²): Exceptional beam quality, resulting in fine cuts and high detail accuracy.
- Cooling Method: Often air-cooled, reducing maintenance complexity.
- Wavelength: Operates at a wavelength of around 1.06 micrometers, making it highly efficient for cutting metals.
Nd:YAG Laser Cutting Machines
Nd:YAG (neodymium-doped yttrium aluminum garnet) lasers are a type of solid-state laser. These machines are renowned for their high peak power and ability to cut through thick materials.
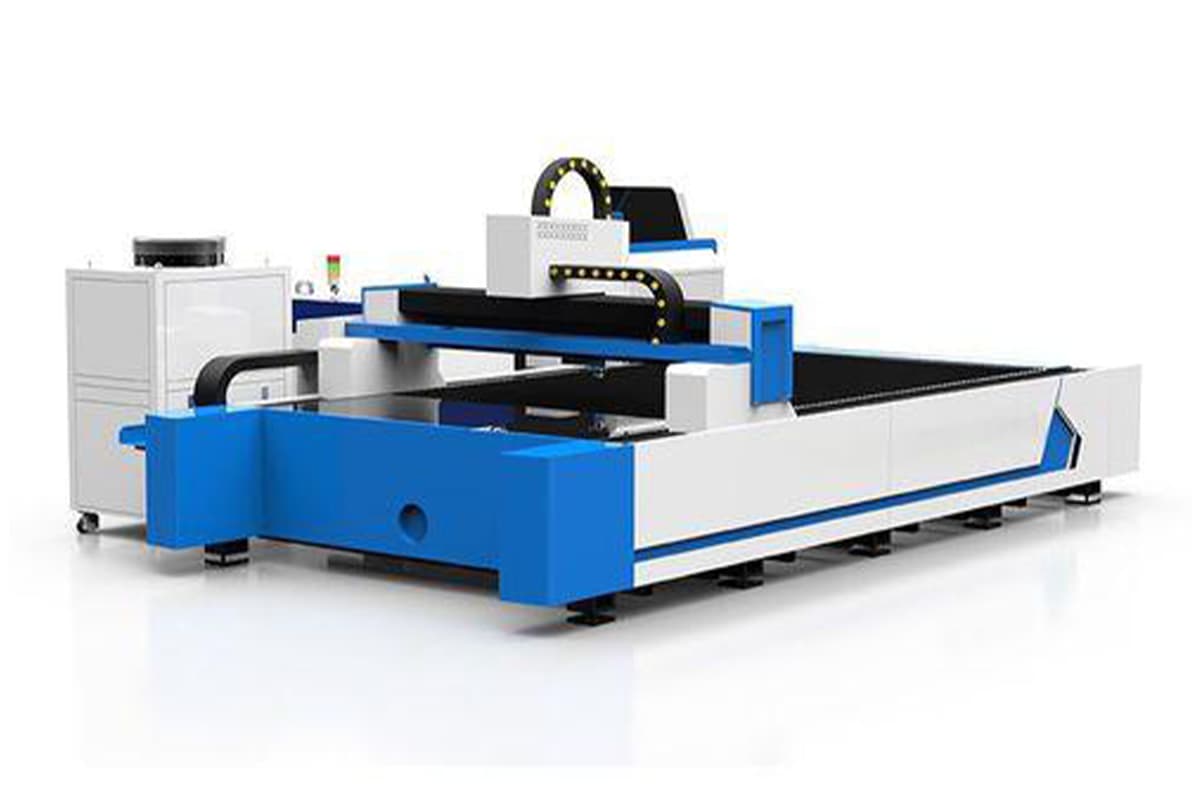
Common Applications
Nd:YAG lasers find major applications in industries requiring high precision and power, such as automotive, defense, and aerospace. They are often used for welding, deep engraving, and cutting thick metals.
Key Specifications
- Power Output: Typically ranges from a few watts to several kilowatts, depending on the application needs.
- Cutting Speed: Generally slower than fiber lasers but very effective for thicker materials.
- Beam Quality (M²): Good beam quality, though not as high as fiber lasers.
- Cooling Method: Usually requires complex water-cooling systems.
- Wavelength: Operates at a wavelength of 1.064 micrometers, effective across various metallic materials.
III. Key Specifications of Laser Cutting Machines
Selecting the right laser cutting machine hinges on a thorough understanding of key specifications. These specifications not only impact the machine's performance but also determine its suitability for specific applications. Below are the critical specifications to consider when evaluating laser cutting machines.
1. Power Output
The power output of a laser cutting machine, measured in watts (W), is one of the most fundamental specifications. It dictates the machine's ability to cut through materials of varying thicknesses and densities. Higher power outputs extend the machine's capability to handle thicker and tougher materials. For instance:
Power Range | Suitable Materials | Typical Applications |
Low Power (10W - 100W) | Thin materials like paper, cardboard, thin plastics | Engraving, precision cutting in electronics and jewelry |
Medium Power (100W - 500W) | Moderate thickness materials like wood, acrylic, metals up to 1/4 inch | Signage, automotive parts |
High Power (500W - 2000W) | Thicker materials, including metals up to 1 inch thick | Cutting metals |
Ultra High Power (2000W - 6000W or more) | Thick metals like steel and aluminum | Industrial applications (shipbuilding, heavy machinery) |
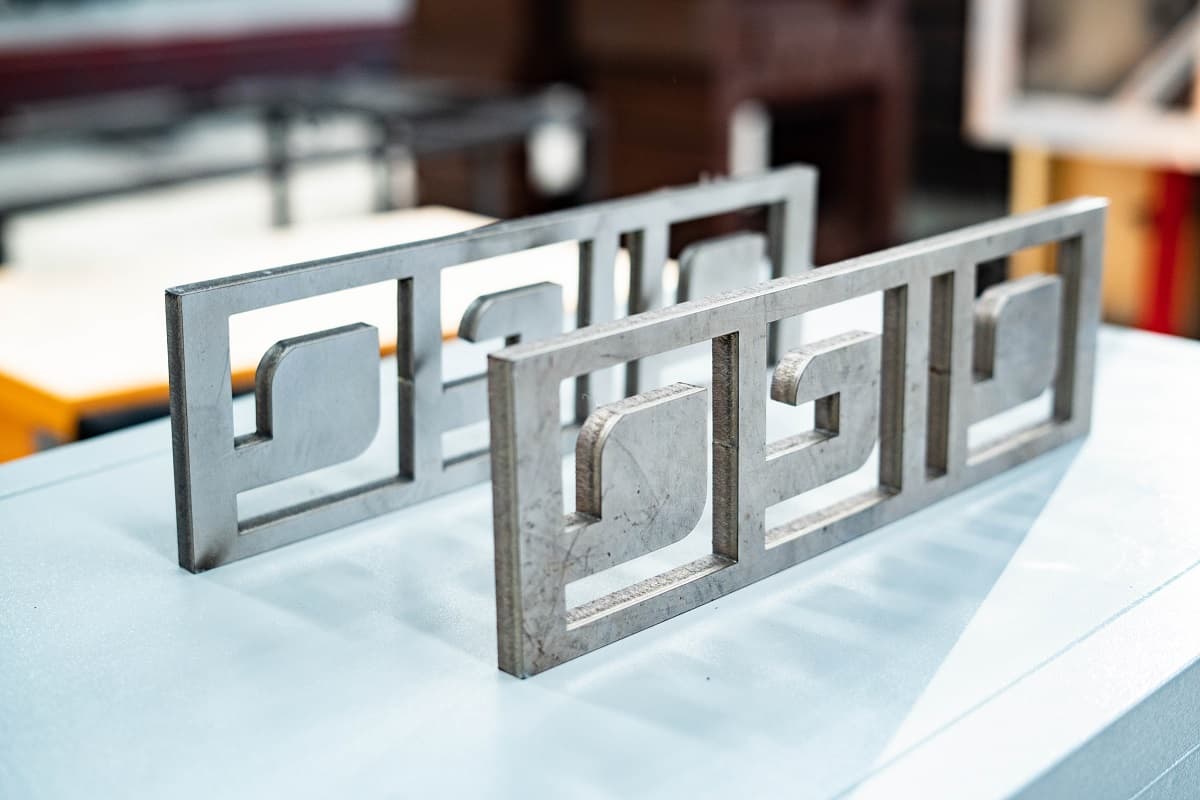
2. Cutting Speed and Precision
Cutting speed, often measured in meters per minute (m/min), determines the efficiency of the laser cutting process. The speed varies significantly depending on the material type and thickness, as well as the machine's power output.
High cutting speeds are beneficial for high-volume production environments, where minimizing cycle time is crucial. However, achieving the optimal balance between speed and quality is key, as excessive speed may compromise cut quality.
Factors Affecting Speed
Several factors influence the cutting speed of a laser cutting machine:
- Material Type:Â Different materials absorb laser energy differently, affecting cutting speed. Metals generally require slower speeds compared to non-metals.
- Material Thickness:Â Thicker materials require more time to cut through, reducing overall speed.
- Laser Power:Â Higher power lasers can cut through materials faster.
- Beam Quality:Â A higher quality beam results in more efficient energy transfer and faster cutting.
Accuracy and Tolerance Levels
Precision involves both accuracy—how closely the cut matches the design—and tolerance—the permissible deviation from the desired dimensions.
High-precision laser cutting machines can achieve tolerances as low as ±0.001 inches, making them suitable for applications requiring intricate detailing and exact measurements.
3. Beam Quality (M²)
Beam quality, denoted by the M² factor, reflects how the laser beam maintains focus over distance. A lower M² value indicates a higher quality beam capable of producing finer, more precise cuts.
This specification is critical for applications requiring high precision and smooth edges, such as in the manufacturing of medical devices and intricate components.
4. Wavelength
The wavelength of a laser affects its interaction with different materials. For instance:
- CO2 lasers: Operate at 10.6 micrometers, making them highly effective for non-metallic materials like wood, glass, and plastics.
- Fiber and Nd:YAG lasers: Operate at around 1.06 micrometers, which are particularly efficient for metal cutting due to their ability to focus on smaller spot sizes, leading to higher precision and faster processing.
5. Cooling Method
Laser cutting machines generate significant heat during operation, necessitating efficient cooling systems to maintain optimal performance and prevent damage. Two primary cooling methods are used:
- Water Cooling: Used in high-power laser systems, especially CO2 lasers and powerful fiber lasers, water cooling systems help dissipate the substantial heat generated during extended or high-power cutting. These cooling systems ensure stable operation by maintaining the optimal temperature, preventing overheating and potential damage to the laser.
- Air Cooling: Suitable for lower-powered lasers, typically those below 150W. Air-cooled systems are simpler and more affordable, making them common in desktop or compact models. While effective for smaller machines and tasks, air cooling is inadequate for larger machines or operations involving heavy-duty cutting.
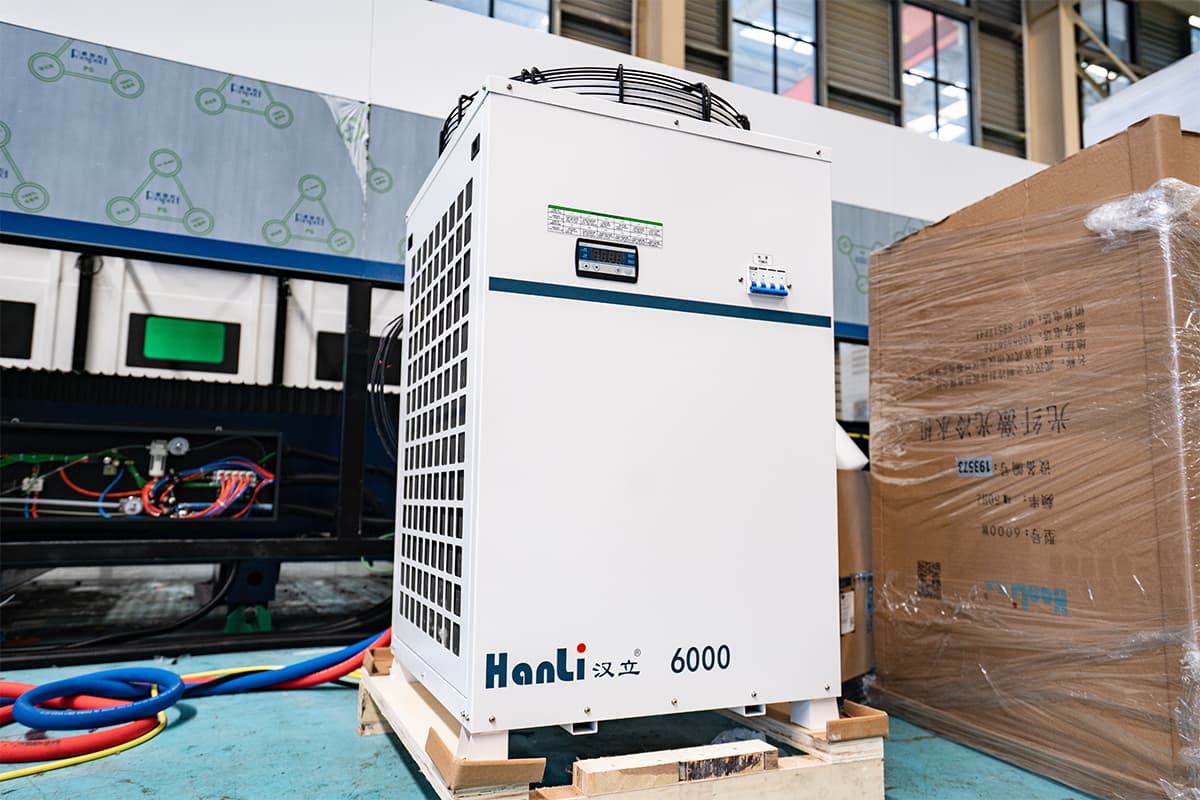
6. Work Area Size
The size of the work area varies between different laser cutting machines and determines the maximum dimensions of the material that can be processed.
Larger work areas are beneficial for applications requiring the cutting of expansive materials, such as in the aerospace and automotive sectors. Conversely, smaller work areas are suited for detailed work on smaller components.
Table Size and Cutting Area
- Small Format Machines:Â Typically have a table size of 300mm x 500mm, suitable for small parts and detailed work.
- Medium Format Machines:Â Offer a work area of around 1,000mm x 1,500mm, ideal for medium-sized projects.
- Large Format Machines:Â Feature table sizes exceeding 2,000mm x 3,000mm, enabling the processing of large sheets and extensive projects.
Impact on Project Size and Scalability
The work area dimensions impact the scalability of your projects. Larger cutting areas allow for the processing of bigger parts or multiple smaller parts simultaneously, increasing production efficiency and reducing setup times.
7. Material Compatibility
The ability to process different materials is a critical consideration. Laser cutting machines should be assessed for their versatility in handling various substrates like metals, plastics, wood, and composites.
Specific machines might be better suited for certain materials—CO2 lasers excel with non-metals, while fiber lasers are preferred for metals.
Types of Materials That Can Be Cut
- Metals:
- Examples:Â Steel, aluminum, brass, copper.
- Best Laser Type:Â Fiber and YAG lasers.
- Non-Metals:
- Examples:Â Wood, plastic, glass, textiles.
- Best Laser Type:Â CO2 lasers.
Thickness Limits
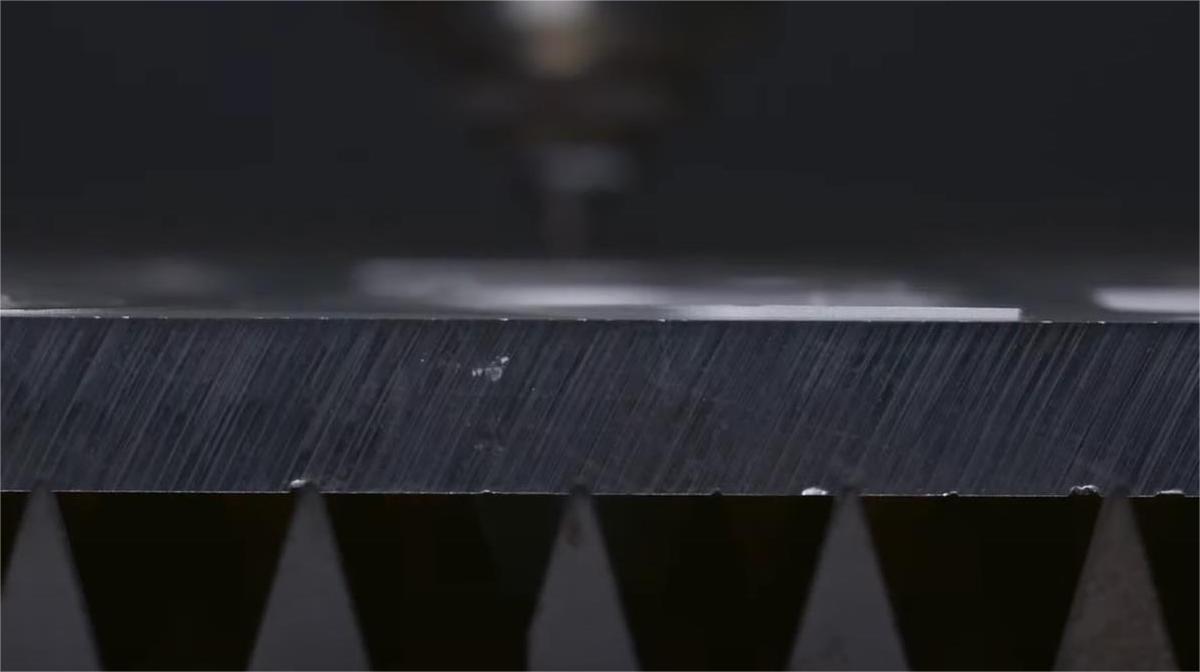
The maximum thickness a laser cutting machine can handle depends on its power output and the type of laser. For instance:
- CO2 Lasers:Â Typically cut non-metals up to 25mm and metals up to 5mm.
- Fiber Lasers:Â Can cut metals up to 30mm with higher power models.
- Nd lasers: Ideal for thinner materials, usually up to 10mm.
8. Maintenance Requirements
Regular maintenance is essential to ensure the longevity and efficiency of laser cutting machines. Key maintenance considerations include:
- Frequency of Maintenance: High-powered machines and those using complex cooling systems typically require more frequent maintenance.
- Cost of Consumables: Items such as lenses, nozzles, and gas supplies need regular replacement. The frequency and cost of these consumables can significantly impact the overall operational cost.
9. Environmental Impact
Modern laser cutting machines are designed with environmental sustainability in mind. Key aspects include:
- Energy Efficiency: Machines with higher efficiency reduce energy consumption and operational costs.
- Emission Control: Systems that effectively manage particulate and gas emissions, thereby ensuring compliance with environmental regulations and enhancing workplace safety.
10. Drive System
- Stepper Motor: Utilized in entry-level or lower-end laser cutting machines, stepper motors provide moderate precision and are sufficient for most small to medium-sized cutting tasks. These motors operate by moving in discrete steps, making them less smooth than servo motors but still reliable for less demanding applications.
- Servo Motor: Found in higher-end, professional machines, servo motors offer significantly greater precision, speed, and smooth movement. Servo motors include a feedback system that allows for real-time monitoring and adjustments, leading to higher accuracy and faster operation. These motors are essential for intricate designs and cutting thick materials quickly and efficiently.
11. Software
Most laser cutting machines come with software tailored for specific operations. Software plays a critical role in translating designs into precise cutting paths and controlling machine behavior. Here are the typical software solutions:
- RDWorks, LaserCut, and LightBurn are commonly used software programs, offering interfaces for adjusting parameters and preparing files for cutting.
- Compatibility with common design file formats such as DXF, AI, SVG, and PLT is essential. These formats allow users to import files from CAD and design software like AutoCAD, Illustrator, CorelDRAW, and others, ensuring flexibility in design preparation.
12. Support Gases
Laser cutting often requires auxiliary gases to assist in the cutting process, especially for metals:
- Oxygen: Commonly used for cutting mild steel. Oxygen helps to oxidize the material during cutting, speeding up the process and improving cut quality, especially for thicker materials.
- Nitrogen: Used primarily for cutting stainless steel and aluminum, nitrogen prevents oxidation by forming an inert atmosphere. This results in a clean, shiny edge without the discoloration or corrosion that oxygen might cause.
- Air: Air can be used for cutting non-metals like wood, acrylic, and plastics. It’s cost-effective and useful for basic cuts in materials that don't require the precision or cleanliness associated with nitrogen or oxygen.
13. Control System
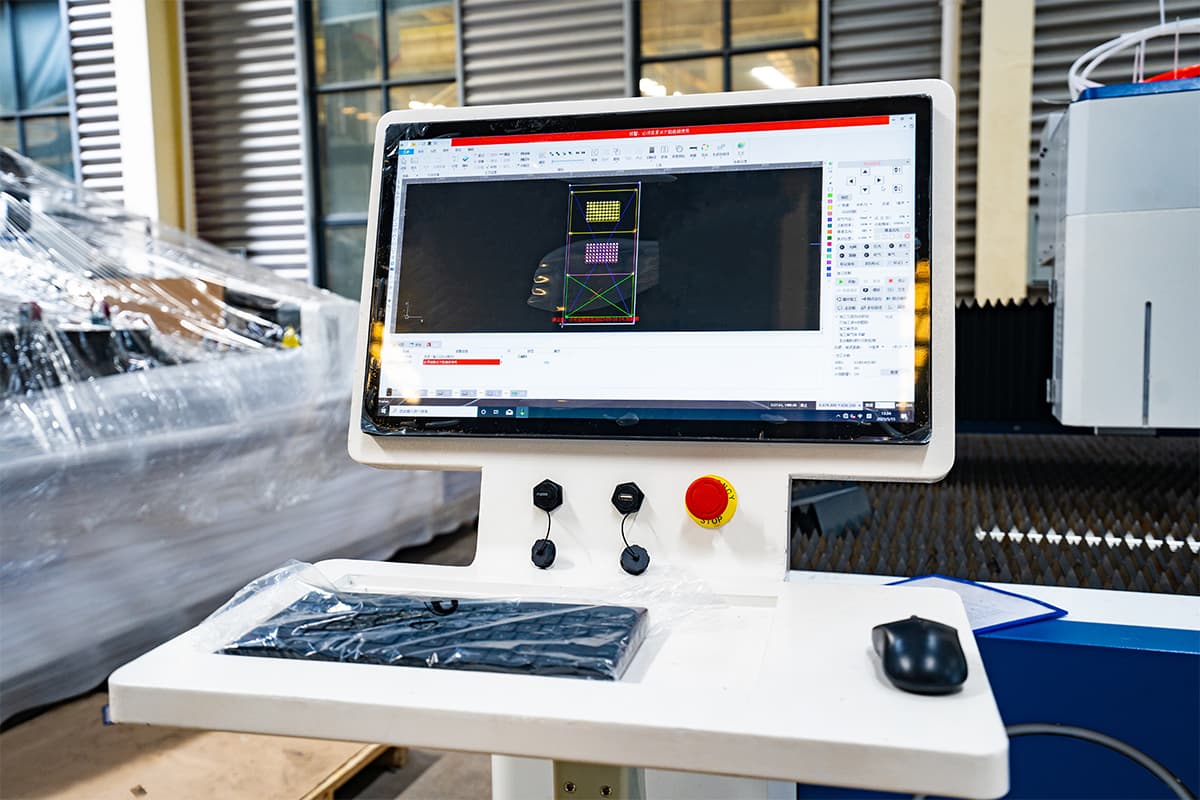
Laser cutting machines are typically equipped with CNC (Computer Numerical Control) systems that allow for fully automated control of the cutting process.
The control system of a laser cutting machine is the interface through which operators manage cutting parameters, design inputs, and operational commands. The CNC system converts the design into machine-readable instructions, precisely controlling the movement of the laser across the workpiece:
- Touchscreen interfaces: Many modern machines come with user-friendly touchscreens for easy operation. These systems allow users to adjust parameters, monitor the cutting process, and even load designs directly onto the machine.
- Advanced Interfaces: High-end machines may feature more sophisticated interfaces, enabling custom settings, remote control, and integration with advanced manufacturing systems.
IV. Evaluating and Choosing a Laser Cutting Machine
Choosing the right laser cutting machine is crucial for ensuring optimal performance, efficiency, and cost-effectiveness in your manufacturing processes. Here, we outline a systematic approach to evaluating and selecting the most suitable laser cutting machine for your specific needs.
Define Your Requirements
The first step in selecting a laser cutting machine is to clearly define your production requirements. This involves considering factors such as:
- Material Types: Identify the primary materials you intend to cut. Different lasers are optimized for different materials; for example, a fiber laser is more suitable for metal cutting, while a CO2 laser excels with non-metallic materials.
- Thickness Range: Determine the range of material thicknesses you will be working with, as this will influence the required power output of the laser.
- Precision and Quality: Assess the level of precision and quality needed for your finished products. High-precision applications, such as those in medical device manufacturing, may require lasers with superior beam quality and fine-detail capabilities.
- Production Volume: Consider your production volume to determine the necessary cutting speed and efficiency. High-volume production may benefit from machines with faster cutting capabilities and automated features.
Assess Technical Specifications
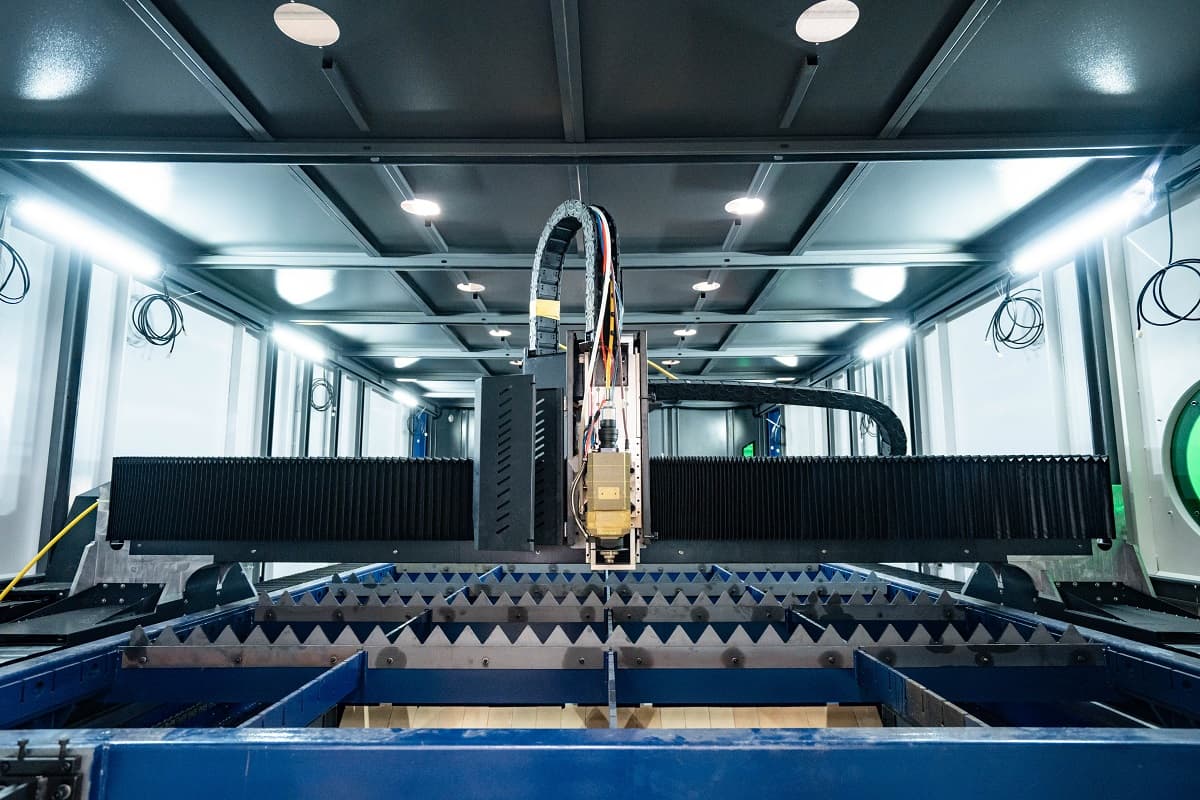
Reference the key specifications outlined in the previous section to evaluate potential laser cutting machines. Key aspects to focus on include:
- Power Output: Matches the power output with the thickness and type of materials you will be processing.
- Cutting Speed: Select a machine with a cutting speed that balances efficiency with quality for your specific applications.
- Beam Quality: Ensure the machine offers the required beam quality for the precision and smoothness of cuts you need.
- Wavelength: Confirm the machine's wavelength suitability for your primary materials.
Evaluate Operational Costs
Operational costs significantly impact the total cost of ownership and should be carefully evaluated. Consider the following aspects:
- Initial Investment: Compare the upfront costs of different machines, including any required accessories and installation fees.
- Maintenance Costs: Factor in the frequency and cost of maintenance, including consumables such as lenses, nozzles, and gas supplies.
- Energy Consumption: Estimate the energy costs associated with running the laser cutting machine. More energy-efficient models may offer long-term savings.
- Downtime: Consider the potential downtime for maintenance and repairs. Machines that are easier to maintain may offer higher reliability and productivity.
Analyze Software and Control Systems
The control system of a laser cutting machine significantly influences usability and integration into your existing workflows. Evaluate the following:
- User Interface: The interface should be intuitive and user-friendly, enabling operators to easily set parameters and monitor operations.
- Software Compatibility: Ensure the machine's software is compatible with your design and production systems. Look for features such as CAD/CAM integration and support for common file formats.
- Automation Capabilities: Advanced features like automated loading and unloading, real-time monitoring, and CNC integration can enhance productivity and reduce manual intervention.
Consider Environmental and Safety Standards
Compliance with environmental and safety standards is critical. Assess the machine's environmental impact, focusing on:
- Energy Efficiency: Opt for machines designed to minimize energy consumption.
- Emission Controls: Ensure the machine has effective systems for managing emissions and particulates, safeguarding operator health and reducing environmental impact.
- Safety Features: Verify that the machine includes necessary safety features such as enclosed cutting areas, emergency stop buttons, and appropriate shielding to protect operators from laser exposure.
Vendor Reputation and Support
Choosing a reliable vendor can make a significant difference in your overall experience. Consider the following:
- Reputation: Research vendor reputation through customer reviews, case studies, and industry references.
- Support Services: Evaluate the level of support offered, including warranty terms, training, and technical assistance. A vendor that offers comprehensive post-sale support can ensure smooth operation and quick resolution of any issues.
- Availability of Spare Parts: Ensure the vendor can supply necessary spare parts promptly, minimizing potential downtime.
Conduct Trials and Demos
Before making a final decision, it is advisable to conduct trials or demos of potential machines. This hands-on evaluation can provide insights into the machine's performance, ease of use, and suitability for your specific applications.
- Sample Processing: Request sample cuts on your materials to assess cut quality and performance.
- Operator Feedback: Involve your operators in the trial process to gather feedback on the machine's usability and features.
Final Decision and Implementation
Based on the comprehensive evaluation, choose the laser cutting machine that best meets your requirements. Plan the implementation process, including site preparation, installation, and operator training, to ensure a smooth transition and optimal utilization of the new equipment.
By following this systematic approach, you can make an informed decision that aligns with your operational needs, maximizing the efficiency and quality of your laser cutting processes.
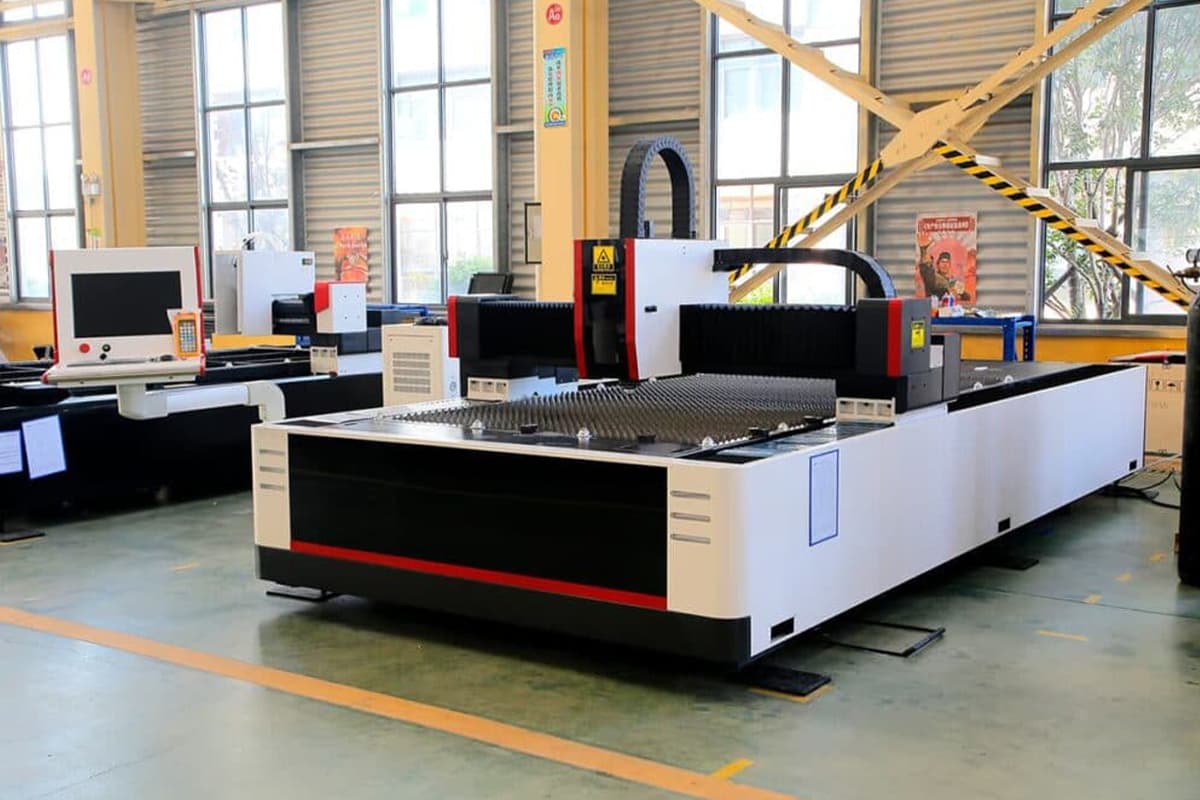
V. FAQ
1. What is the difference between CO2 and fiber laser cutting machines?
- CO2 Lasers: Utilize a gas mixture (primarily carbon dioxide) as the lasing medium. They operate at a wavelength of 10.6 micrometers, making them highly effective for cutting non-metallic materials such as wood, plastics, and textiles. Despite being versatile enough for some metal cutting, they often require additional assists like oxygen to cut thicker metals effectively.
- Fiber Lasers: Employ a solid-state lasing medium, where the laser is transmitted through an optical fiber. Operating at a wavelength of around 1.06 micrometers, fiber lasers excel in metal cutting, including reflective materials like copper and aluminum. They offer higher efficiency, faster speeds, and lower maintenance requirements compared to CO2 lasers.
2. How do I determine the right power output for my needs?
Determining the right power output involves assessing your specific cutting requirements:
- Material Thickness: Higher power outputs (such as those above 2kW) are necessary for cutting thicker materials. For instance, industrial applications involving heavy steel or aluminum require high-powered lasers to ensure clean cuts.
- Material Type: Different materials require varying power levels. Metals generally need more power, while non-metals like wood and plastics can be efficiently cut with lower-powered lasers.
- Precision Needs: If your application demands high precision (like fine engravings or detailed metal cuts), opting for a machine with suitable power and excellent beam quality is crucial.
- Production Volume: For high-volume production, a balance between power and speed is vital to maintain efficiency and throughput.
3. How often does a laser cutting machine need maintenance?
Maintenance frequency largely depends on the type of laser cutting machine and its usage:
- Routine Checks: Conduct daily inspections of lenses, nozzles, and gas pressures to catch early signs of wear or misalignment.
- Scheduled Maintenance: Typically, a detailed maintenance check should be performed every few hundred operational hours, as per the manufacturer’s guidelines. This includes cleaning optics, checking cooling systems, and calibrating the laser beam.
- Consumable Replacement: Regularly replace consumables like lenses, mirrors, nozzles, and assist gases to maintain optimal cutting performance.
4. What should I look for in laser cutting machine control software?
When selecting control software, consider the following features:
- User Friendliness: An intuitive interface that simplifies operation and reduces training time.
- Programming Flexibility: Support for various programming languages and compatibility with existing CAD/CAM software.
- Real-Time Feedback: Provides real-time monitoring and diagnostic capabilities to optimize cutting parameters and detect issues promptly.
- Automation Integration: Compatibility with automated systems and robotics to enhance production efficiency.
- Security Features: Robust security measures to protect against unauthorized access and ensure data integrity.
Artificial Leaf Hair comb,Hawaii Foam Flower Hair Comb,Hawaiian Hula Dance Hair Decoration
Xuzhou Kylin Craft & Gifts Co., Ltd. , https://www.kylincraftandgifts.com