Runner system plays a very important role in injection molding process. The mission of runners is to deliver melt from injection nozzle to the cavities. A quality runner design is very helpful in improving product qualities. However, traditional cold runner systems have certain inherent issues, such as material waste, regrind problem, and increased cycle time. Moreover, poor product cosmetics, such as welding line and low gloss matter, are commonly seen with the use of traditional cold runner. As a result, hot runner technology has been widely applied in order to cope with these issues in injection molding process. It can provide the benefits of reduced injection pressure/clamping force, easy cavity filling, decreased cycle time, improved product quality, and energy/material saving. The application product fields include many large-sized plastic parts, such as bumper, automobile dashboard, TV/LCD front/back cover and also some common plastic products: bottle caps, food plastic containers and so on.
A hot runner system is mainly composed of hot runner gate, hot nozzle, manifold, heating coil and so on. Their designs have a great influence on the hot runner system performance. However, the mechanism in the hot runner system is so complicated that certain critical issues, such as temperature control and uniformity, flow imbalance, and material overheating, still exist in the current hot runner technology. As a result, a simulation technology is in great demand for hot runner designers and makers to predict potential problems before the real manufacturing.
With Moldex3D’s latest technology in advanced hot runner analysis, hot runner designers and makers are able to investigate melt temperture, pressure drop, shear heating effect, and moldbase temperature distribution dynamically in the hot runner systems. These simulating results are very useful in understanding complex hot runner system and finding potential issues in their hot runner designs. As a result, it is an indispensable tool in optimizing hot runner system designs and improving product qualities with the less real mold trials, cost, and development time.
Figure 1 shows the preprocessing for hot runner analysis. The CAE model can be created without too much effort in Moldex3D eDesign. Each major hot runner component is imported, attribute set, and meshed automatically. Also, heat conduction faces can be defined in a very convenient way to match real boundary conditions. The STL format of heating elements or cooling channels is supported for complex layouts. The integration of filling, packing, cooling and warpage analysises provides a more accurate prediction on injection molding process and product qualities.
Figure 2 shows the analysis results for runner and moldbase temperature. The clipping and slicing functions can be used to easily observe the temperature behavior everywhere inside the melt channel and moldbase. The multiple outputs or animations show the dynamic response for designers to track back the history of the hot runner system. For more information regarding advance hot runner module and case studies, please go to our website www.moldex3d.com to find out more in-depths.
Here, we also include one technical paper concerning the investigation into melt temperature in a real hot runner system and experimental verification.
(a) The CAE model with manifold,hot runner nozzle etc
(b)The heating elements in the CAE model
(c) Define heating conduction faces
Fig. 1 Preprocessing Hot Runner Analysis
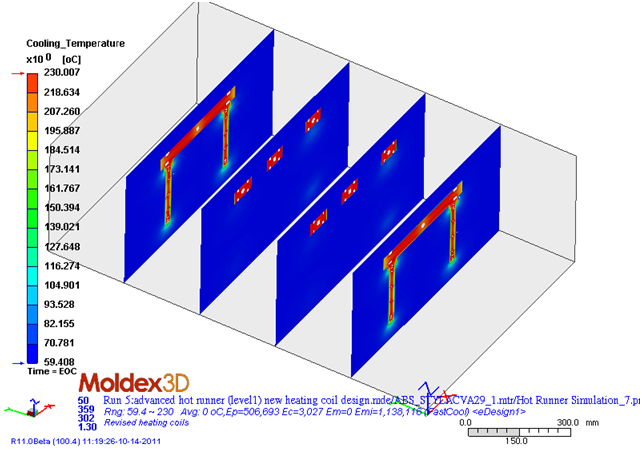
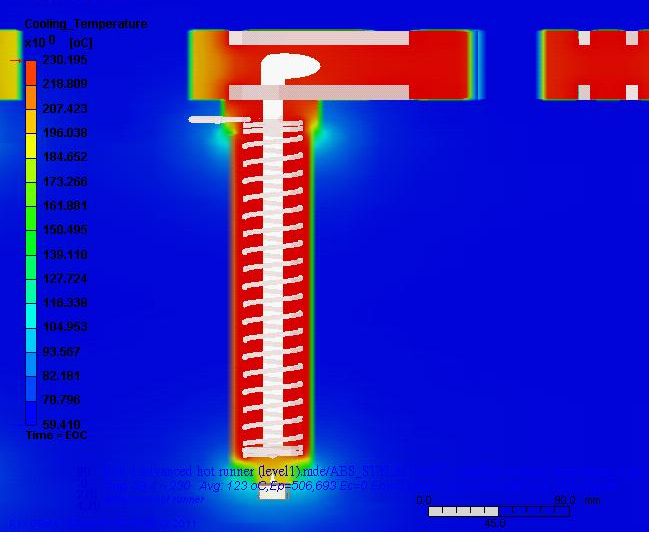
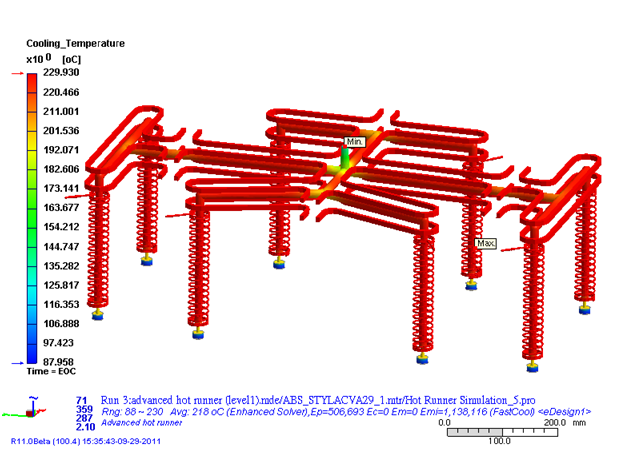
Fig. 2 Â Runner and Moldbase Temperature Profile
Jiangsu Jinyihao Metal Science And Technology Co., LTD , https://www.jyhshelf.com