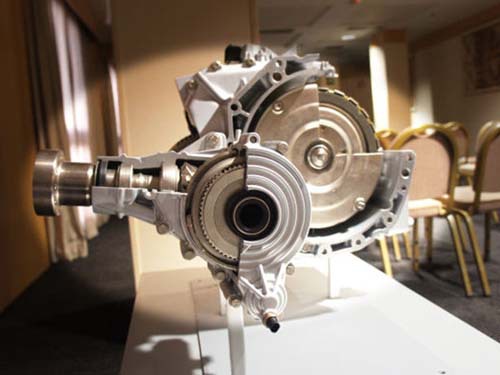
ZF has made a great contribution to the field of drive system electric drive: ZF's electric vehicle drive products for small and medium-sized cars are well adapted to future urban traffic conditions. Its drive unit is mounted in the middle of the axle and has a maximum output of 120 kilowatts, which ensures high torque values ​​at low speeds. And, its power supply is integrated with the electric drive device. ZF introduced a new configuration of the drive concept, the enhanced version: the power supply is integrated in the drive bridge and the output power is increased to 120 kilowatts. The wheel-side electric-driven electric torsion beam (eTB) is another electric drive technology developed by ZF. It integrates a semi-independent suspension system into a transmission system. The left and right wheels each have a compact drive system. Integrate the transmission and the motor in a single aluminum housing.
The core of the ZF electric drive module is an asynchronous motor that eliminates the need for grounded materials with rare elements such as helium or neon. In addition, such a device also includes a compact single speed ratio transmission mechanism, power supply and a set of control programs. Thanks to the two-stage deceleration gear mechanism and the innovative high-speed design, the ZF electric drive system can achieve speeds of up to 21,000 rev/min, as well as high power conversion efficiency and excellent performance. When the vehicle is just starting up, the electric drive system can generate 17,00 Nm of torque so that the vehicle can complete 100 km of acceleration within 9 seconds. The peak power of this drive system is 90 kW.
High power conversion efficiency
For many pure electric vehicles, the electric motor and the inverter work together to generate a certain amount of energy loss in a particular driving condition, and the ZF electric drive device solves this problem. ZF has improved the power conversion efficiency by 6% by optimizing the performance of the complete electric drive system. The electric drive device weighs about 45 kilograms and sets a weight bar in the equivalent output product. ZF continues to develop it to further increase its output/weight ratio.
Continuously improve motor performance
ZF has adopted a new version of the enhanced version of the electric drive system: the output power of the electric motor has been increased to 120 kW and 2,500 Nm. Integrated power supply is a major feature of this device. At the same time, ZF is also developing a modular system for each output level to better meet the needs of different customers and vehicles. In the future, ZF's electric drive system will no longer apply only to small cars and compact cars, but will rely on axle hybrid powertrains to further extend the product line to mid- to high-class front-wheel drive cars.
Electric wheel-driven electric torsion beam (eTB)
The core of the electric wheel-driven electric torsion beam (eTB) is the integration of the semi-independent suspension system with the drive system: the left and right wheels each have a compact drive system that integrates the transmission and the motor in a single, lightweight aluminum housing. In addition, the use of multi-faceted pressure bonding technology to achieve the link between the aluminum thrust bar and the steel cross structure is another highlight of this project.
ZF's innovative technology is specifically developed for mini cars and small cars. Its single motor unit provides 40 kW of power and a total output of 80 kW. If you need to install an additional third motor, its requirements for loading space are the same as before. Two independent drive motors can more accurately distribute torque for a single wheel, enhancing vehicle safety and improving vehicle handling. The design of the electric wheel-driven electric torsion beam (eTB) follows the lightweight and high-speed design of the ZF central electric drive module. At the same time, the loading of the motor does not have a significant effect on the unsprung mass of the vehicle.
The integrated design of the electric wheel-driven electric torsion beam (eTB) effectively saves installation space. For example, the central motor is directly fixed to the vehicle body, eliminating the need for additional mechanical drive components, thereby effectively freeing the vehicle's central loading space and providing a space for automobile manufacturers to personalize designs. The connection point between the device and the body is similar to that of a conventional axle system, so that it can be easily connected with the existing technology module. In addition, it can also match the brake system and standard hub size used in traditional models.
Industrial aluminum profiles refer to aluminum alloy materials used in industrial production and construction fields, which have the characteristics of corrosion resistance, and easy processing. Industrial aluminum profiles have many advantages, such as light weight,high strength and good thermal conductivity.In addition, industrial aluminum profiles also have good plasticity and can be processed and assembled through processes such as extrusion and stamping to meet different design requirements. Industrial aluminum profiles have a wide range of applications in industrial production and construction fields. It can be used to manufacture structural components of mechanical equipment, guide rails for conveying equipment, and frames for automation equipment. Due to its excellent performance and flexible design, industrial aluminum profiles have been widely applied and promoted in various fields.
Industrial Aluminum Profile,Heat Sink Extruded Aluminium Frame,Anodized Heatsink Aluminium Profile,Extruded Heatsink Aluminum Profile
FOSHAN WINKAI ALUMINIUM CO.,LTD , https://www.wkaluminum.com