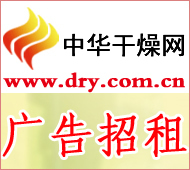
The PVC industry in Australia has basically eliminated the use of lead stabilizers in PVC products.
According to the progress report of the 2011 PVC product management plan released in May, the PVC industry in Australia has reduced the use of such stabilizers by 99% since the industry plan was first introduced in 2002 to reduce the environmental and health impact of PVC.
According to the report, the PVC industry is about to achieve its goals within the entire industry and continue to make progress on the issue of PVC life cycle.
The Australian PVC industry started this initiative spontaneously in 2002. The plan takes into account the impact of PVC on the environment and human health in the production, use and disposal of PVC. About 80% of PVC manufacturing companies in Australia, plus some important suppliers of raw materials and additives and many importers of PVC products have signed the plan.
The management of the plan was established in June 1998 and is headquartered in Melbourne, Australia, Vinyl Association (VCA).
In 2011, 11 of the 31 signing companies fully met all the goals they had promised. One of the signing companies was delisted this year for failing to submit the report as scheduled, and another six new companies joined the program.
VCA Chief Executive Sophi MacMillan said that the PVC industry has made further commitments outside of production, including stricter emission standards for PVC emulsion resins. In addition, the energy efficiency and greenhouse gas emissions charter established in 2011 was also included in the plan.
The use of molds has a life span. When the use of a pair of molds exceeds its life span, the molds should be replaced in time, so the mold production process has certain repeatability.
Milling, boring, drilling, reaming, tapping and other processes are also used in regular mold processing.
The main material of the mould is high-quality alloy steel. Some moulds with a long service life are often made of Crl2, CrWMn and other ledeburite steels. The production and processing of this material is very strict, so the processing process cannot be ignored. The thermal deformation treatment is also an aspect that needs to be taken seriously in the processing. To sum up, when selecting the airport, the processing conditions should be met as much as possible, such as strong functionality, high accuracy of machine tool, good rigidity, good thermal stability, and anti-type function.
Some surface shapes are composed of multiple curved surfaces, such as automobile cover parts, aircraft, parts, toys, household appliances, etc., so the surface of the mold cavity is very easy to be complicated, and some can be processed through mathematical calculation.
Some molds have neither drawings nor data in the production process, and can only be imitated through physical objects, which requires high imitation accuracy and no deformation.
Household Plastic Mold ,Plastic Household Mould,Plastic Spoon Injection Molding Machine,Plastic Spoon Machine
Ningbo Chenwei Machinery Technology Co.,Ltd , https://www.chenweimachine.com