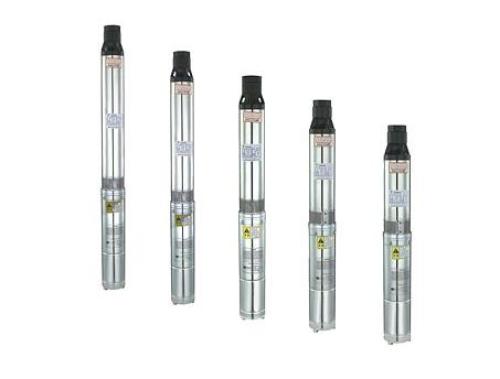
1, the working principle and performance characteristics
The submersible pump is a universal water-lifting machine in which the motor and the water pump are directly integrated into the submerged water. Its working principle is that the electric motor drives the impeller to rotate at a high speed through the pump shaft, performs work on the liquid under the action of the centrifugal force, and converts the mechanical energy into a liquid. The energy, the liquid (water) flies outwards from the impeller, and the ejected liquid gradually becomes slower in the diffusion chamber of the pump casing, the pressure gradually increases, and then flows out of the outlet pipe of the pump outlet. The starting point for the design of the submersible pump is “no winding or blockingâ€. Some models also have a tearing mechanism or a cutting device that can tear long fibers and ribbons in water and discharge them. The innate weakness of submersible pumps is that the medium they pump is mostly soft, and the amount of sediment in the water is limited to less than 3%. When the sediment concentration is large, it is easy to damage the seal. Once the motor enters the water, the bearings and windings are damaged. The motor burned.
2, installation and use
Submersible pumps generally have certain requirements on the upper and lower deviation ranges of the power supply voltage and frequency. For high-powered submersible pumps, a step-down or soft start must be used to reduce the impact on the power grid or other electrical equipment and the submersible pump itself. The installation and use of the submersible pump should be based on the correct selection of the environment and pay attention to related matters.
2.1. Selection and use environment
The selection of submersible pumps should be properly selected according to the characteristics of working conditions. The main considerations in selecting the type of flow include the flow, head, and installation methods. Only when the selected lift is close to the actual head required, the pump can operate efficiently and energy-saving. Improper selection will have a great impact on the operation of the pump.
In general, the use environment of deep well submersible pumps should meet the following requirements:
(1) Three-phase AC power supply with a power frequency of 50 Hz and a rated voltage of ±5% tolerance;
(2) The solid content (by mass) is not more than 0.01%;
(3) The inlet of the pump must be below the water level lm, but the depth of diving should not exceed 70m below the static water level, and the depth of the bottom of the pump from the bottom of the well should be at least lm;
(4) It is required that the well is vertical and the well wall is smooth, and the well pipe must not be staggered.
2.2, installation
The installation of the deep well submersible pump must first check the power supply line, grid voltage, frequency, and whether the control switch meets the conditions of use; secondly, the water pump must take good grounding measures; check the installation of the electric control cabinet is correct and well grounded; check the lifting facilities should be safe and reliable. The installation of the pump is performed in the following order:
(1) Remove the water filter net located in the middle of the water pump, unscrew the water injection screw plug and the water release screw plug, fill the machine with clean neutral water, and then tighten the screw plug. Check for leaks at each motor connection and seal if leaked.
(2) Measure the motor insulation resistance with a 500-volt megohmmeter at no less than 150 megohms, and use a screwdriver to rotate the impeller.
(3) First connect the short water pipe to the check valve body, install a plywood under the upper flange of the short water pipe, then gently lift the water pump and put it into the well so that the plywood seat falls on the well cover.
(4) Use another splint to clamp the long water pipe and suspend it to connect it with the short water pipe. Then remove the first pay plate to lift another long water pipe. Repeat the installation and complete the well cover to fix the splint. In the manhole cover, the curved water pipe, valve, outlet pipe and deep well submersible pump are installed.
(5) In the process of installation, the pipe gaskets shall be placed between the two flanges of the pipeline, and the bolts shall be tightened symmetrically. The cables shall be bundled in the groove on the flange of the water pipe; the cable lines shall not be treated as The use of slings, but not allowed to damage the cable.
2.3. Use matters needing attention
The installation and operation of deep well submersible pumps need to pay attention to:
(1) When lifting, care should be taken to protect the cables to prevent breakage. The lifting devices (such as tripods, hoists, or electric hoists, etc.) used should be larger than the submersible pumps and have enough room. Before hanging, manually turn the impeller to check whether the rotation is flexible, whether the contact of the main contactor is in good contact, whether the cable and the cable connector are broken or scratched, and whether the grounding of the motor housing is reliable, and check the three-phase line conduction condition with a multimeter.
(2) Start the submersible pump, it should be smooth, no vibration and abnormal sound, observe the motor running current and line voltage before and after the start of significant fluctuations. Pay attention to the submersible pump that is operated after the first installation or inspection. If the submersible pump is found to be abnormal, it can only be started immediately to observe. If the submersible pump is found to be abnormal, it should be stopped immediately. Check whether the direction of rotation is correct and whether the installation is proper. run.
3, analysis of the causes of common faults
There are six kinds of common failures in the use of deep well submersible pumps in the following situations:
(1) No serious pumping or head shortage: At this time, the pump will not turn when it turns, and when the submersible pump is idle, there will be more noise. This phenomenon is mostly the bearing damage of the submersible pump.
(2) Bad seal: The shaft end of the water pump motor has a double-end mechanical seal part, which is made of high wear-resisting material. After the submersible pump is used for a period of time, the seal leaks due to wear or natural aging and the seal leaks. Oil seepage. In addition http://, in each mechanical mating surface has a round rubber seal to form a gasket to prevent water penetration in the pump body, but due to the high speed of the motor used in the submersible pump, in the long-term use will inevitably cause serious mechanical seal face wear .
(3) Breakage of water outlet pipe Leakage: The sound of the normal rotation of the submersible pump pump wheel suspended in the deep well (the electric meter rotates normally), but it cannot pump water or only a small amount of water. This is mostly out of water. The tube is damaged.
(4) Card pump: The water pump does not turn, but it can hear a buzzing sound, which is mostly because the pump impeller is stuck by foreign matter. For example, due to geological reasons, our school has caused a large amount of sand in the well water to easily cause damage to the filter cover.
(5) Leakage current: Leakage is one of the most common faults of the water pump. The fault phenomenon is that when the knife is closed, the leakage protector in the power distribution room will automatically trip, which is caused by the water in the pump body of the submersible pump. Leakage phenomenon.
(6) Startup capacitor failure: When you connect to the power supply, you can hear the sound of squeaking. The full-color LED display but the submersible pump motor does not turn; if the impeller is gently toggled, the submersible pump can turn immediately and it can be judged as a capacitor. Damaged.
4, maintenance methods
In order to ensure the normal and reliable operation of deep-well submersible pumps, prolong their service life, and reduce accidents during their use, maintenance and maintenance of submersible pumps must be strengthened, and maintenance and repairs of submersible pumps and their control systems should be carried out regularly, at least once a year. Preventive testing.
4.1, routine maintenance
The maintenance of the submersible pump mainly includes mechanical and electrical aspects. The mechanical maintenance focuses on the sealing and prevention of corrosion. The electrical inspection focuses on the cable insulation and prevention of leakage.
4.1.1 Routine Mechanical Maintenance
(1) Always check the mechanical seal of the submersible pump. Check all kinds of seals, such as seals, filler screws, seal boxes, etc., and repair or replace worn parts and components with poor sealing performance. If it is found to loosen, it must be tightened in time. If the seal is not strong, replace the new one in time to ensure safe use.
(2) To prevent the occurrence of corrosion of the submersible pump. If the surface of the pump is damaged and removed, remove the rust immediately and apply anti-rust paint to protect it.
(3) Regularly check the bearing status of the submersible pump to see if the bearing is worn, if it is short of oil, if there is a running inner race or a running outer race, and if it needs to be replaced.
(4) The submersible pump is generally required to conduct a comprehensive inspection and maintenance every two years. The sound of the mechanical operation can be used to initially check whether the components of the submersible pump are normal. Check whether the impeller is worn or cavitation, whether the shaft is rusted or deformed or worn, whether the fastening screws inside and outside the motor are loosened, and whether there is sediment or plugging in the pump port and around.
4.1.2, Routine maintenance in electrical aspects
(1) Regularly check the resistance of the submersible pump to the ground and check whether the cable is damaged; if it is damaged, replace it in time to prevent leakage;
(2) Always check the operating voltage and current of the submersible pump. The three-phase voltage measured by the voltmeter should be basically the same;
(3) During the operation of the pump, it must be observed whether the meter reading and the vibration and sound of the pump are normal. If an abnormal situation is found, it must be dealt with promptly.
4.2 Inspection of Common Faults
Due to the frequent operation of deep well submersible pumps used in this school, working hours are longer every day. Therefore, once a year (in a special case, once every semester), the disassembly test of the pump is performed. For common failures, perform corresponding maintenance according to the following different conditions:
(1) No serious pumping or head shortage: most of the bearings of the submersible pump have been damaged. At this time, the upper and lower screws on the submersible pump can be unscrewed, and then the turbine wheel and rotor can be taken out and the bearing can be tapped gently. Then replace the same type of bearing.
(2) Bad seal: When the seal box leaks, there will be traces of oil at the water inlet section. You can unscrew the screw and check if the oil chamber has been filled with water. If the oil chamber is filled with water, you must use a new seal box. . When replacing, remove the pump cover, remove the accessories such as impeller, bakelite, gasket, water thrower, etc., then remove the water inlet section, remove the key and bushing on the shaft, and detach the sealing piece of the sealing box. Replaceable sealed boxes.
(3) The structure of the embedded communication front-end unit of the outlet pipe power system and its application Broken leakage: Replace the outlet pipe or take emergency measures for plugging.
(4) Startup capacitor failure: Replace the same size capacitor.
(5) Card pump: Mostly, the impeller of the pump is stuck by foreign matter. The center screw of the impeller can be unscrewed and the foreign matter such as the sand and the impeller removed.
(6) Leakage current: This is due to the phenomenon of leakage of the motor winding caused by water in the submersible pump pump body. Waterproof tape can be used for winding waterproofing, but pay attention to soak a few hours later and use a rocking table to check the insulation. Replace or replace the main cable with no repair value.
Our firm introduced whole set of good-sized numerical control hydraulic folding equipment(1280/16000) as well as equipped with a series of good-sized professional equipments of armor plate-flatted machine, lengthways cut machine, numerical control cut machine, auto-closed up machine, auto-arc-weld machine, hydraulic redressing straight machine, etc. The firm produces all sorts of conical, pyramidal, cylindrical steel poles with production range of dia 50mm-2250mm, thickness 1mm-25mm, once taking shape 16000mm long, and large-scale steel components. The firm also is equipped with a multicolor-spayed pipelining. At the meantime, for better service to the clients, our firm founded a branch com. The Yixing Jinlei Lighting Installation Com, which offers clients a succession of service from design to manufacture and fixing.
Street Lighting Pole, Solar Power, Solar Lighting Pole
Jiangsu Xinjinlei Steel Industry Co., Ltd. , http://www.steel-pole.com