-40ºF PDP 2.6m3/min Desiccant Air Dryer |
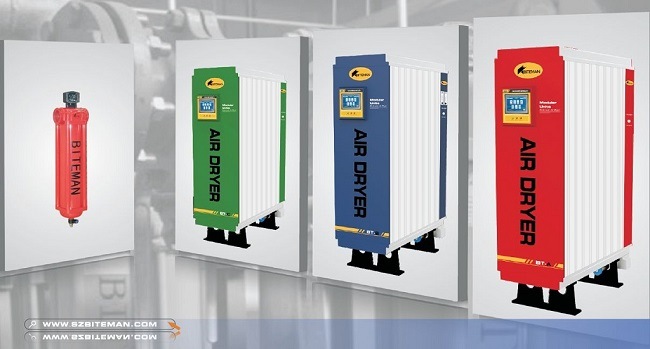
Features
1. Less than 5% purge air without auxiliary equipment, 012KW power consumption 2. Pressure and inlet temperature is digital readout on screen; purge air gauge allows manually control regeneration air according to the wanted pressure dew point 3. Small desiccant chambers' group, each chamber unit is independent and detachable 4. Replace with factory filled desiccant chamber, ease of maintenance and constant pressure dew point -40ºC (-40ºF) is ensured 5. The lowest operation cost, user could recoup dryer investment in three years by saving huge air and electricity 6. 1/3 size to traditional dryer 7. The shortest downtime 8. Using Molecular sieve as desiccant |
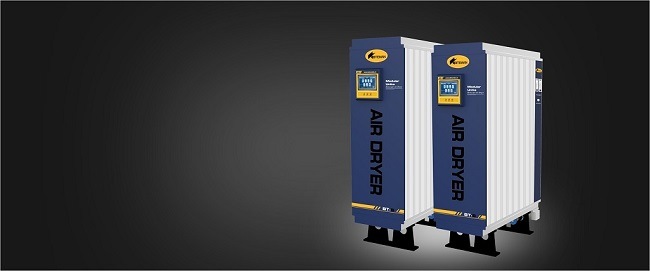
How it works
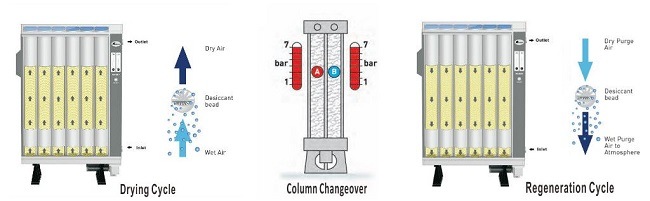
Drying cycle
The process air enters the dryer through the inlet and is directed into the on-line drying chamber via the inlet valves and lower manifold. The air is evenly distributed through the drying units and passes over the desiccant material, reducing the water vapour content. The dried process air then combines in the upper manifold and exits the dryer via the outlet check valves |
Column changeover
Before the on-line (drying) and off-line (regenerating) columns change over, the dryer exhaust valve, is closed, allowing the purge air to re-pressurise the off-line columns. This ensures a consistent system pressure and dewpoint when the drying chambers change over. |
Regeneration cycle
At the start of the regeneration cycle, the exhaust valve of the dryer is closed and the off-line chamber is at full line pressure. The air in the off-line chamber has a dewpoint equal to the air leaving the dryer. The exhaust valve is then opened and the dry air within the chamber expands rapidly as it leaves the dryer via the exhaust silencer, forcing water to be removed from the desiccant material. Once the off-line chamber has de-pressurised, a continuous bleed of dried process air is directed into the off-line upper manifold. This air is known as purge air. With the exhaust valve open, the purge air expands from line pressure to atmospheric pressure and flows downwards through the columns, over the off-line desiccant material. As the purge air at line pressure contains a fixed amount of water vapour, allowing it to expand means the purge air becomes even drier, increasing its capacity to remove water from the saturated desiccant bed. |
Details of advantages
Innovative structure with patents, adopts small desiccant chamber unit  1. Air flow equally and evenly pass through each desiccant chamber 2. Avoid channeling effect which more likely happens in traditional desiccant dryer 3. Small chamber allow no pressure vessel annul inspection 4. Molecular sieve capability is much better than Alumina and silicon desiccant in traditional dryer 5. Easy to maintain and replace factory filled desiccant chamber unit, ensure good performance as beginning 6. PLC controller, Full function touch panel control |
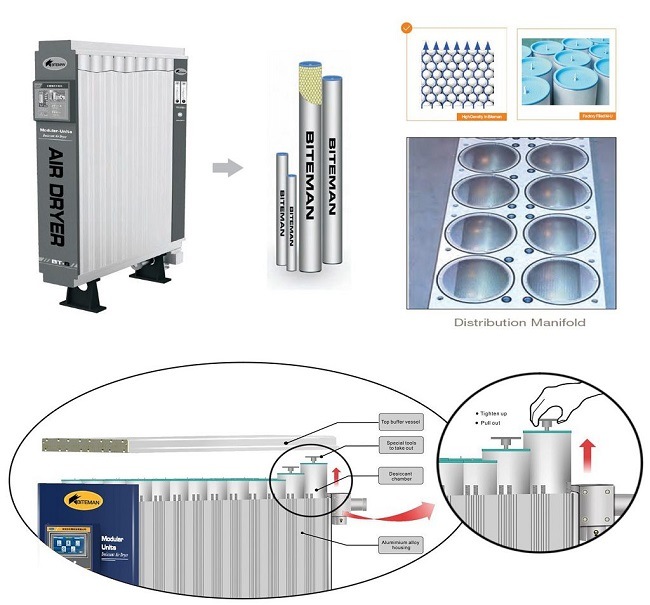
Product details
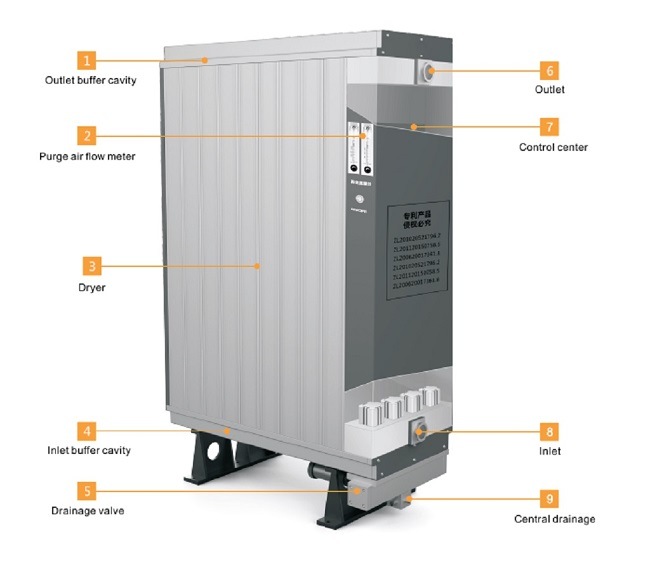
Specification data
BTGMXW-B Series | Heatless | |||||||
Model | Pipe Size (inch) | Flow Range(m³/min) | Dimension(mm) | Weight(kg) | ||||
@5~6bar | @6~7bar | @7~10bar | L | W | H | |||
BTGMXW015-B | G1 | 1.1 | 1.3 | 1.5 | 380 | 240 | 828 | 78 |
BTGMXW026-B | G1 | 1.9 | 2.3 | 2.6 | 380 | 240 | 978 | 87 |
BTGMXW038-B | G1 | 2.7 | 3.3 | 3.8 | 486 | 240 | 978 | 106 |
BTGMXW065-B | G2 | 4.8 | 5.8 | 6.5 | 486 | 240 | 1628 | 159 |
BTGMXW085-B | G2 | 6 | 7.4 | 8.5 | 595 | 240 | 1628 | 192 |
BTGMXW106-B | G2 | 7.4 | 9.1 | 10.6 | 703 | 240 | 1628 | 226 |
BTGMXW146-B | G2 | 9.8 | 12 | 14.6 | 920 | 240 | 1628 | 293 |
BTGMXW165-B | G2 | 11.6 | 14.2 | 16.5 | 1029 | 240 | 1628 | 327 |
BTGMXW206-B | G3 | 14.6 | 17.8 | 20.6 | 1250 | 240 | 1628 | 380 |
BTGMXW248-B | G3 | 16.7 | 20.5 | 24.8 | 829 | 480 | 1628 | 510 |
BTGMXW295-B | G3 | 21.5 | 26.3 | 29.5 | 938 | 480 | 1628 | 574 |
BTGMXW336-B | G3 | 24.1 | 29.5 | 33.6 | 1047 | 480 | 1628 | 638 |
BTGMXW385-B | G3 | 26.8 | 32.8 | 38.5 | 1156 | 480 | 1628 | 702 |
BTGMXW425-B | G3 | 29.7 | 36.4 | 42.5 | 1265 | 480 | 1628 | 767 |
BTGMXW465-B | G4 | 32.7 | 40.1 | 46.5 | 1374 | 480 | 1628 | 831 |
Installation
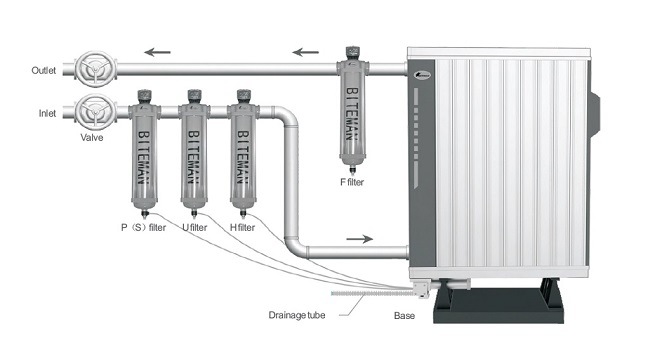
About Biteman technology
Biteman technology, the leading supplier and manufacturer of high efficiency desiccant air dryer and filter in China, with the advantages in low consistence PDP -40ºF, high efficiency 5% purge air, and easy to maintain, has widely applied for GM/P&G/Gree/BYD all over the world.  Contact us today to learn more. www.bitemantech.com |
Â
Our Diesel Water Pump Set,can be choose Deutz/Cummins/Ricardo Diesel Engine Driven Self-Priming Pump Set For Irrigation(Manufacturer)/Water Pump Generator/Hose Pump/Water Pump Set Product introduction: P series self priming non-clog centrifugal sewage pump is a new generation product which develop on the basis of the lastest technology and craftwork. Because of the reliable performance, its life lasts more than 20 years. We take special usage of the sewage pump into consideration on design, so we add a hole to make sure that stronger sewage can be cleaned quickly when pump is jammed. The unique lubrication oil mechanical seal cavity makes the performance more reliable and avoids to damage mechanical seal when it operates without water. To ensure a smooth operation, low noise, long life, all the main components such as imported bearing, to overcome the traditional inherent shortcomings such as low flow rate capacity, difficult to install, difficult maintenance and frequent failure. P series self-priming Pump has the character of strong anti-clogging. In order to avoid towels, bags and so long fiber pollution caused by debris blocking the sewage pump sewage poor. We Design will cut down pollution-pore structure In front of the pump to ensure that the debris can be cleared more quickly. There is a big vortex chamber play important role. It is no need to equip check valve in the inlet and outlet to sewage efficiently when the pump separately completely. Main usage: 1. Municipal Project, Sewage Project, Instruction Project 2. Transportion of the sewage of uptown 3. Sewage transportion in Hospital, hotel and so on 4. Classification of municipal sewage treatment factory and concentrate treatment systems engineering. 5. Transportation of the factory and contaminated water Operation condition: 1. The temperature of medium no more than 80° C, the density of medium is 1.0~1.3*103 Kg/m3, PH is within 5~9, 2. Max diameter of solid should be less than 75 mm, 3. Max suction lift no more than 7 m
Diesel Water Pump, Diesel Engine Water Pump, Diesel Engine Water Pump Set, Diesel Water Pump Set
Weifang Huatian Diesel Engine Co., Ltd , https://www.enginepart.nl