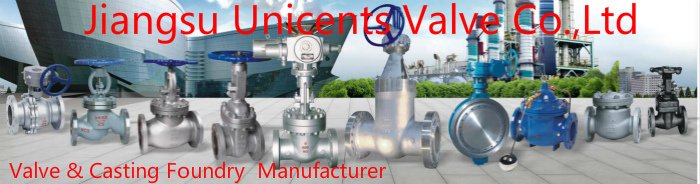
                                                    Â
Product Description
Â
Product Name | API Cast Steel Pressure Seal Swing Check Valve |
Material | A351 CF8M/CF8/CF3, A216 WCB, A352 LCB/LCC |
Size | 1/2''~12'' (Â DN15~DN300) |
Certificate | CE API |
Port | Full Port |
Working Pressure | 1.0~6.4Mpa |
Connection Ends | flange |
Working Temp. | -40ºC~300ºC |
Suitable Medium | Water, Steam, Oil and some corrosive liquid etc. |
Seal | PTFE, RPTFE, PPL |
Type of connection | BW RTJ RFÂ ETC. |
Inspection &Â Testing | API598;API-6D |
Company Profile
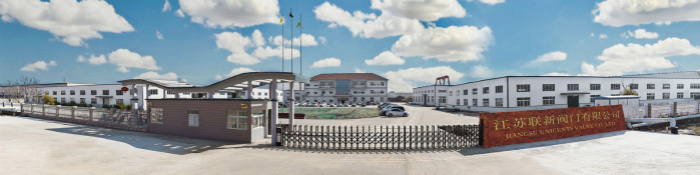
JIANGSU UNICENTS VALVE CO.,LTD is one of the valve manufacturers with experience for over 20 years. Its site occupies 85,370M2,equipped with latest technology&advanced CNC machine,assembling,testing,packing,chemical&physical analysis workshops. Its annual out of Valves is about 3,000,000 sets and casting foundry is 20,000 tons. Supported by capability of casting industry,which helps maintain our on time delivery,ensure superior quality and cost-efficient. We unicents are ready ,looking forward to your sincere co-operation and mutual development.
Â
Workshop Info.
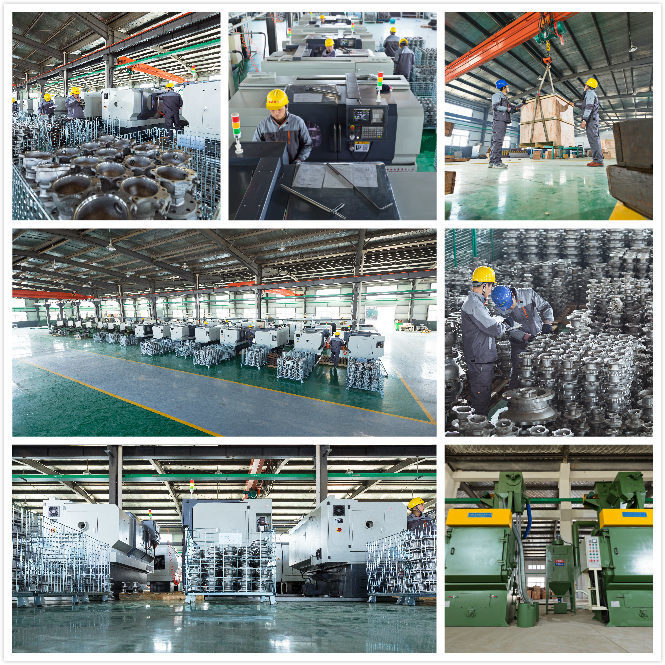
FAQ
Q:Why choose us ?
A: we are a manufacturer, we have been manufacturing valve over 20 years .
B. We have our own casting foundary of a large scale
Q. what is your payment term?Â
 A: T/T , L/C or other acceptable payment.
Â
Q:Can we print our logo on your products?
A: yes, we offer OEM/ODM service, we support the customized logo, size, package,etc.
Â
 Q: what is your main market?
A: North America, South America, Eastern Europe, Southeast Asia, Africa, Oceania, Mid East, Eastern Asia, Western Europe
Â
Q: Can I get samples from your factory?
A: Yes, Samples can be provided.
Â
Q: If products have some quality problem, how would you deal with?
A: We will responsible for all the quality problems.
Â
Q:How about your capacity?
A:We have 300staffs,own 50 CNC machines,and five persons  in charge of quality inspection and 5 engineers. Our 6 casting block workshops can both ensure on time delivery and quality that last.
Delivery Condition
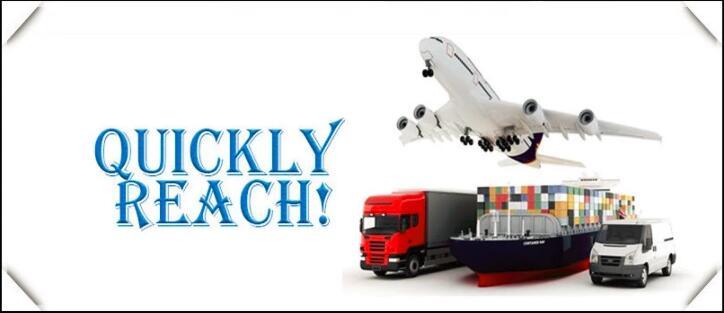
Â
Delivery Time | 15~30 Days |
Package | Standard Exporting Plywood Case |
Shipping Port | Qingdao/Shanghai, China |
Shipping Terms | EXW, FOB, CFR, CIF, etc. |
Payment Terms | T/T, Western Union, PayPal, etc.  30% prepayment, 70% balance paid before shipping or against copy of BL |
Advantage | OEM/ODM is applicable;Our own casting room |
Others | We also manufacture Flange Ball Valve, Gate Valve, Globe Valve, Check Valve, Butterfly Valve &Â Y Strainer |
Contact Info.
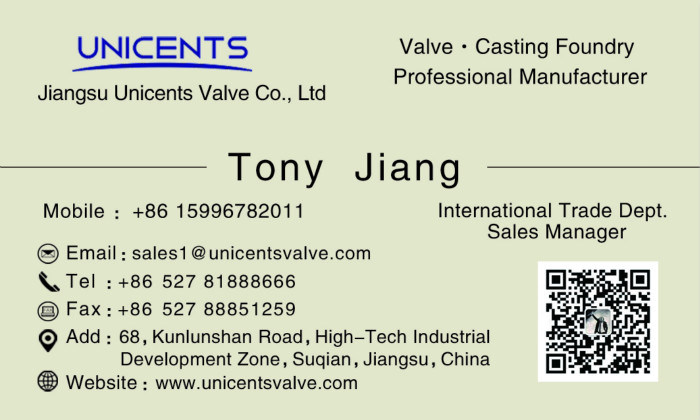
Â
The Die Castings that are created in this process can vary greatly in size and weight, ranging from a couple ounces to 100 pounds. One common application of die cast parts are housings - thin-walled enclosures, often requiring many ribs and bosses on the interior. Metal housings for a variety of appliances and equipment are often die cast. Several automobile components are also manufactured using die casting, including pistons, cylinder heads, and engine blocks. Other common die cast parts include propellers, gears, bushings, pumps, and valves.
Die casting is a manufacturing process that can produce geometrically complex metal parts through the use of reusable molds, called dies. The die casting process involves the use of a furnace, metal, die casting machine, and die. The metal, typically a non-ferrous alloy such as aluminum or zinc, is melted in the furnace and then injected into the dies in the die casting machine. There are two main types of die casting machines - hot chamber machines (used for alloys with low melting temperatures, such as zinc) and cold chamber machines (used for alloys with high melting temperatures, such as aluminum). The differences between these machines will be detailed in the sections on equipment and tooling. However, in both machines, after the molten metal is injected into the dies, it rapidly cools and solidifies into the final part, called the casting. The steps in this process are described in greater detail in the next section.
Die cast parts can vary greatly in size and therefore require these measures to cover a very large range. As a result, die casting machines are designed to each accommodate a small range of this larger spectrum of values. Sample specifications for several different hot chamber and cold chamber die casting machines are given below.
Type | Clamp force (ton) | Max. shot volume (oz.) | Clamp stroke (in.) | Min. mold thickness (in.) | Platen size (in.) |
Hot chamber | 100 | 74 | 11.8 | 5.9 | 25 x 24 |
Hot chamber | 200 | 116 | 15.8 | 9.8 | 29 x 29 |
Hot chamber | 400 | 254 | 21.7 | 11.8 | 38 x 38 |
Cold chamber | 100 | 35 | 11.8 | 5.9 | 23 x 23 |
Cold chamber | 400 | 166 | 21.7 | 11.8 | 38 x 38 |
Cold chamber | 800 | 395 | 30 | 15.8 | 55 x 55 |
Cold chamber | 1600 | 1058 | 39.4 | 19.7 | 74 x 79 |
Cold chamber | 2000 | 1517 | 51.2 | 25.6 | 83 x 83 |
The selection of a material for die casting is based upon several factors including the density, melting point, strength, corrosion resistance, and cost. The material may also affect the part design. For example, the use of zinc, which is a highly ductile metal, can allow for thinner walls and a better surface finish than many other alloys. The material not only determines the properties of the final casting, but also impacts the machine and tooling. Materials with low melting temperatures, such as zinc alloys, can be die cast in a hot chamber machine. However, materials with a higher melting temperature, such as aluminum and copper alloys, require the use of cold chamber machine. The melting temperature also affects the tooling, as a higher temperature will have a greater adverse effect on the life of the dies.
Materials | Properties |
Aluminum alloys | ·Low density |
·Good corrosion resistance | |
·High thermal and electrical conductivity | |
·High dimensional stability | |
·Relatively easy to cast | |
·Requires use of a cold chamber machine | |
Copper alloys | ·High strength and toughness |
·High corrosion and wear resistance | |
·High dimensional stability | |
·Highest cost | |
·Low die life due to high melting temperature | |
·Requires use of a cold chamber machine | |
Zinc alloys | ·High density |
·High ductility | |
·Good impact strength | |
·Excellent surface smoothness allowing for painting or plating | |
·Requires such coating due to susceptibility to corrosion | |
·Easiest to cast | |
·Can form very thin walls | |
·Long die life due to low melting point | |
·Use of a hot chamber machine | |
Advantages: | ·Can produce large parts |
·Can form complex shapes | |
·High strength parts | |
·Very good surface finish and accuracy | |
·High production rate | |
·Low labor cost | |
·Scrap can be recycled |
Die Casting,Aluminum Die Casting,Die Casting Parts,Zinc Die Casting
Ningbo City Yinzhou Ruican Machinery Co.,Ltd , https://www.factoryforging.com