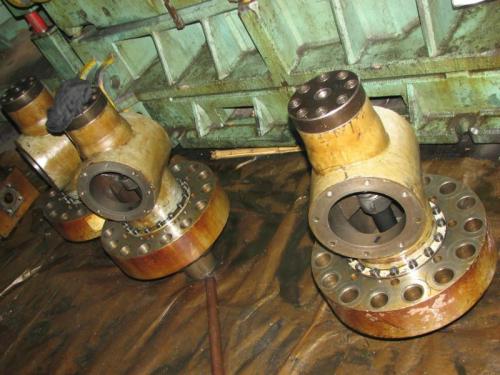
In general, the mechanical press has a simple structure, fast production cycle and high efficiency, and is suitable for large-volume, simple blanking molding processing. The hydraulic press is suitable for medium and small batch production, has the requirements of JIT, the shape is changeable, and the speed, pressure and position requirements of the slider are more accurate, and the production mode is based on the order processing.
Now, the productivity requirement is lower, and the blanking of small and medium-sized parts generally uses a hydraulic press, and its production cycle time generally does not exceed 20-40 pieces per minute. According to the size of the workpiece, the pressure load (centering or eccentricity) and the forming method determine the structure of the press is a C-frame, double-column or four-column press, and the fuselage structure must be able to withstand the impact vibration caused by blanking.
C-shaped single-column presses will skew the angle-wave mode during punching, and the four-column press machine will deflect the path of its force's action point from its geometric center, while the double-column press has a stable structure with precise movements and is rarely biased. Oblique, suitable for eccentric load processing.
Designers often design the weight of the blanker press twice as much as the standard configuration to improve its robustness and reduce the impact of blanking.
It is ideal to use a hydraulic press in the blanking process that meets the following requirements.
â—† It is difficult to find out the benefits of using a hydraulic press only if you know the slider stroke range and whether the pressure control adjustment meets the machining requirements. When designing the press, if the stroke range is set, the hydraulic press should be selected. Similarly, setting the preload on the hydraulic press is also very simple. Pre-compression is used to counteract the weight of the workpiece or the shock of an emergency stop.
â—†Buffering function (pressing the double-piece may cause damage to the press)
When two pieces of material are given to the mold when feeding, or when the mold is ejected, the device fails to eject the processed parts. At this time, it is possible to cause double pressure. In this case, the mechanical press may be damaged, and the hydraulic press will not be damaged because it has an overload protection function and limits the maximum pressure.
Hydraulic presses for various configurations are widely used in press processing. The most commonly used are: 20-250 TC single-column presses (small pieces of processing); 50-1000T four-column presses (large and medium-sized parts); double posts Presses (for processing large workpieces with conveyors or eccentric pressurization); less double-column presses with working pressures above 5000T.
The following requirements should be selected for the press hydraulic press â—† large and small pieces of mixed processing â—† high slider and pressure control requirements when different processing speed or position control of the slider, high position accuracy and long requirements When time pressure is maintained, a hydraulic press should be used.
â—†The production beat is slower. When processing small parts (1-2 inches), the beat is 60spm;
When processing large (3-15 inches), the beat is 30-40 spm.
â—† More complex program settings For diversification of product types, complicated program settings are often required, and the hydraulic machine is easy to set up.
â—† Higher frequency of JIT parts replacement With this requirement, the use of a hydraulic press can quickly change settings.
â—† Flexibility for installation When another hydraulic pressure machine is needed for this project, it needs to be reinstalled. For example, when the production line changes, the maximum pressure can be used at any stage of the stroke, and the press can be easily reset.
Deep drawing Because the hydraulic press can accurately control the speed of the slide, the metal material is allowed to move without delay due to the delay. Therefore, the hydraulic press is used for deep drawing. The hydraulic machine is suitable for the following drawing processes: low output, frequent mold change, multiple drawing speeds, large pressure changes in the hydraulic pad, and deep drawing requirements for high pressure adjustment.
Deep drawing is recommended in the following cases.
â—† The frequency of mold replacement is high, and the JIT is required because the hydraulic press is easy to set up and can generally be completed within a few seconds.
â—† When the feeding mechanism uses the hydraulic pad when feeding or automatically discharging the material, the hydraulic machine should be used. â—† The workpiece is more complex and the setup is simple. Due to the complicated workpiece design, the required machining program is also complicated, and the adjustment of the hydraulic machine is simple. In this case.
â—† Press Structure When a single press is required to complete the machining or there are multi-step drawing and shaping operations, a hydraulic press can be used. The hydraulic press is also suitable for single-stretch production with deep drawing and/or reverse stretching. Due to the pressure stroke limitation, it is suitable for finishing molding.
â—† With full pressure, the hydraulic machine can maintain the highest pressure during the stretching process, which can reduce the tonnage requirement of the press.
â—† Feeding mode Feeding mode is manual feeding rather than automatic feeding depending on the processing volume, small batch production (less than 100,000 pieces per year), and artificial feeding; and in mass production, partial or full use Automatic feeding mechanism.
â—† If eccentric pressure is required for eccentric load, double column press should be used.
Conclusion When you decide to purchase a hydraulic press, in addition to assessing several of the factors involved in this article, there are also safety, ease of maintenance, installation cycles, and usage. You should also provide the press supplier with as much specific requirements as you can for press performance.
For manufacturers, the key is: production beats, budget, mold design, workpiece structure, number of mold changes, press size, and the purpose of the project.
The development of science and technology shows that in order to make a correct and wise choice, you must maintain close contact with and communicate with different press manufacturers. Only in this way can a correct selection and full use of a press be made.
This Cow Feed Grass Chopper can be apply to cut all kinds of wet and dry crops, corn stalk ,rice straw, wheat straw ,bean stalk, bean stalk, green grasses ,sorghum stalk etc with big capacity. It is suitable agricultural equipment for cattle,farm,farmer which is feeding cow, horse, sheep, deer, rabit etc.
It is small size,compact steel structure, light weight.
high capacity of feeding port,long range of chaff discharging,high capacity of corn silage making
We can manufacturing electric motor,diesel engine and gas engine type chaff cutter according clients' demand or you can buy motor or engine in your domestic market we will prepare motor or engine frame base for you.
Hammer Mill Grinder,Animal Feed Grass Hammer Mill,Grass Hammer Device,Animal Feed Grinding
XinxiangHexie Feed Machienry Manufacturing Co.Ltd , http://www.hxfeedmill.com