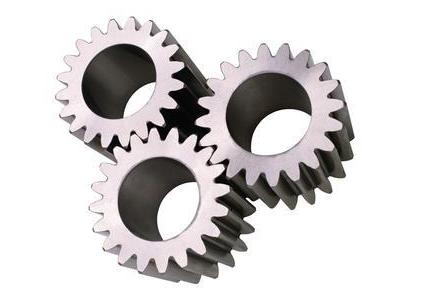
The processing principle is as shown.
The main processing techniques are as follows: (1) After the first annealing, rough cuts are made on the planer (or similar machine tool) according to the dashed line.
(2) Two half gear bolt holes are drilled on the drill press line; the two half tooth blanks are combined into one body by bolts.
(3) Use the lathes to press the inner, outer and end faces of the roughing line.
(4) In order to reduce the deformation error, it is necessary to perform stress relief after the rough machining and a second artificial aging (annealing) treatment.
(5) Correct the overlapping of the two half gears as shown, and evenly weld the two half gears together in the outer circle and the inner hole.
(6) Use the planer to position the A and B surfaces and the C and D surfaces one at a time so that the C surface (the reference surface for measuring the height direction) is perpendicular to the AB surface within 0.05 mm.
(7) Finally, the workpiece is mounted on a movable boring machine and a boring and milling machine table, and the workpiece is lifted with a jack or an adjustable oblique iron, and the AB surface is adjusted to be vertical to the main axis with a tolerance of 0.0050.008mm; and the C surface is measured with a dial gauge. , Tolerance 0.005mm on length L. Then fastened on the bench.
After the AB and C faces meet the requirements, you can start drilling holes in the alignment pins. Pay attention to the order of boring holes when boring holes. That is, the holes A1, A2, A3, and A4 (or B1, B2, B3, and B4) in the vertical direction are first bored, and then the spindle distance L is moved horizontally and then the holes B4, B3, B2, and B1 are sequentially moved. .
The holes in the same vertical position are placed in a coaxial position so that the tolerance L of the pin holes on both gears is exactly the same. Because the spindle only moves up and down at this time, but the left and right direction is fixed. This guarantees the accuracy of the coordinates in one direction. The coordinate in the other direction, that is, the distance moved up and down can be controlled by placing a height scale with a dial gauge on the C surface, measuring the highest point of the spindle, and recording the l1 of the holes A1, A2, A3, and A4. The actual size of l2,l. After completing the A4 hole, keep the height coordinate of the spindle unchanged, and translate the spindle L to reach the position of hole B4. In order to eliminate the error of the C plane, then use the height scale and dial gauge to re-check the actual size of the C plane to the highest point of the outer diameter of the spindle, and put the dial indicator to zero, as the measurement B3, B2, B1 Hole reference point. Do not move the dial indicator at this time. After the completion of B4 hole, the spindle left and right position can not be moved, the spindle only moves up by l distance (note to be consistent with é•— A3, positioning pin hole processing principle A4 hole size error) B3 hole, according to this method Until the end of B2, B1 hole. If the height dimension accuracy is not high, it is better to use a special cylindrical block gauge (ie cylindrical rods with tolerances on both ends) for comparative measurements to ensure the accuracy of l1, l2, l3; another method is to accurately measure with a caliper. The distance between the two sides of the hole is consistent with the corresponding hole spacing of the boring machine diagram assembled by Baoli column and the power head (at this time, attention must be paid to the influence of the aperture error). Of course, this method is affected by the level of boring measurement. In addition, if the C plane is difficult to use as a measurement reference, a high-precision standard square may be fixed on the workbench at two places apart from L as a reference for comparison measurement, or two small angle irons with a perpendicularity of 0.010 mm may be specially prepared. Use the original screw hole on the AB surface to secure the bisection as a measurement reference. In short, no matter which measurement method is used, the position error of the vertical hole can be precisely controlled.
Using a self-producing boring machine to machine the dowel pins If you do not have a spindle-moving boring mill, you can use the column and the power head to assemble two sets of soil-suppressed beds placed at two locations apart from each other. At this time, the positioning accuracy is completely transformed into a high-level measurement problem. When assembling, the vertical guide rail surface and the C surface, etc. should be used to find the vertical and horizontal levels (accuracy 0.010/1000). The verticality of the main axis and the split plane (ie, the AB plane) can be found as shown by the dial indicator. That is, the magnetic table and dial gauge are fixed on the main shaft, and the radius of the adjustment dial position is equal to twice the width of the teeth. When the main shaft is rotated by one hand by hand, the column is adjusted so that the maximum reading of the dial gauge on the main shaft is not greater than 0.005mm. At this time, the parallelism of the two columns is also basically adjusted at the same time. The vertical direction of measurement and control is basically the same as above.
For the machining of other similar holes, the same method as the positioning pin holes can be used.
This device is a special device to cut steel strip rolls into strips with a certain width. It is mainly used for decoiling cutting into strips and coiling of silicon steel sheets and thin steel plates and is applicable to processing and production of plate sheets for transformers, motors and transformers.
Slitting line,Shear Cutting Machine,Steel Strip Shearing Line,Automaic Shearing Line,Shearing Steel Strip Machine
JINAN EURO-ASIA MACHINERY CO., LTD , https://www.eaelectricmachine.com